
Predictive Maintenance: The Game Changer in Food Industry Operations
By The Maintainers • May 13, 2024
What if the key to revolutionizing food industry operations lies in predicting the future of equipment health? That’s where predictive maintenance in the food industry comes in handy.
This is a strategy increasingly vital in the food sector, bridging maintenance with food safety, efficiency, and sustainability. The approach marks a significant shift from the reactive methods of the past to proactive, data-driven strategies.
How come?, you may ask…
Well, by analyzing data trends and machine learning, predictive maintenance (PdM) anticipates equipment failures before they occur, minimizing downtime and reducing waste.
This not only ensures continuous production but also upholds the stringent safety standards crucial in the food industry.
As we delve into how PdM is changing the game, consider its potential to transform your operations and enrich your maintenance strategies.
Now, are you ready to explore how this innovative approach can benefit your business? Stay with us as we uncover the transformative power of predictive maintenance in the food industry.
Decoding Predictive Maintenance in the Food Industry
This proactive strategy involves analyzing equipment data to predict potential failures before they happen, ensuring that machinery is always in top-notch condition.
But why is this so crucial for food production?
In the food industry, equipment reliability directly affects product quality and safety — there’s no room for error.
That’s paramount, no questions asked. Why? According to the World Health Organization, “an estimated 600 million – almost 1 in 10 people in the world – fall ill after eating contaminated food and 420 000 die every year, resulting in the loss of 33 million healthy life years.”
So, in practice, PdM not only prevents unexpected downtime but also maintains the consistency and integrity of food products.
Tell us: With uptime being critical, can you afford to risk a sudden breakdown that could halt production and compromise food safety?
Predictive maintenance it’s a pivotal element in sustaining the seamless flow of operations, guaranteeing that every batch meets the stringent standards expected by consumers and regulators alike.
Harnessing Predictive Analytics for Smarter Food Production
Predictive analytics is the engine driving the new era of smart food production, but what does this mean for the industry? It’s about using data to foresee equipment issues and plan maintenance proactively, ensuring that the production line operates without unexpected interruptions.
But how does this work in practice?
Consider a bakery, where ovens must maintain precise temperatures or a dairy plant where pasteurizers operate continuously.
Predictive analytics can monitor these systems in real-time, detecting anomalies that could indicate a pending failure.
Think with us: Isn’t it better to service equipment based on actual condition rather than a preset schedule?
Moreover, in beverage bottling plants, where conveyor belts and fillers are the lifelines, predictive analytics helps schedule maintenance during planned downtimes, thus avoiding costly disruptions.
By predicting when these key pieces of equipment are likely to fail, maintenance can be performed without affecting the production flow.
Evolution of Maintenance Practices in the Food Industry
The maintenance practices in the food industry have evolved significantly, shifting from reactive to more strategic, predictive approaches.
Initially, maintenance was mostly reactive, dealing with breakdowns as they occurred. Over time, with the advent of preventive maintenance, efforts shifted towards preventing unplanned downtime through regular, scheduled interventions.
The real game-changer has been the adoption of PdM, which uses condition-monitoring tools and real-time data analysis to foresee potential equipment failures.
This approach allows for maintenance to be scheduled at the most opportune times, minimizing production interruptions and associated costs.
In this industry, this evolution is particularly critical due to the need for constant uptime to meet production quotas and comply with strict regulatory requirements.
Maintenance strategies have had to adapt, focusing on maximizing the availability of key production assets and ensuring that maintenance activities do not disrupt critical production periods.
The integration of predictive maintenance in the food industry represents a significant methodological advancement.
Why? Because it ensures equipment reliability, optimizes asset utilization, and maintains product quality, all while adhering to the stringent standards set by food safety regulators.
Key Benefits of PdM for Food Manufacturers
If you think PdM in the food industry is just a technical upgrade, you better think again. We’re talking about a strategic revolution. The reason?
It directly translates to reduced downtime and increased production efficiency.
But how does this impact the bigger picture?
Firstly, minimizing unexpected equipment failures means production lines run smoother and longer, directly boosting output and profitability — knocking a huge goal for most companies.
Additionally, by ensuring machinery is always performing optimally, PdM enhances food safety, a non-negotiable aspect in the industry.
This proactive approach can lead to fewer product recalls and higher compliance with stringent food safety standards — what, in reality, helps protecting consumer health and elevating brand trust.
Cost savings also come into play.
PdM helps avoid the hefty expenses associated with emergency repairs and production halts.
By identifying potential problems before they escalate, manufacturers can plan maintenance activities without disrupting production, ultimately preserving the bottom line.
In essence, the strategic implementation of predictive maintenance can lead to a virtuous cycle of improved efficiency, safety, and trust in the food manufacturing sector.
Strategizing Predictive Maintenance Integration in Food Industry Processes
Finding it hard to implement PdM in your company? Here’s a comprehensive step-by-step:
Technology Integration
Implementing predictive maintenance in the food industry begins with integrating the right technologies.
Are your current systems capable of supporting advanced predictive analytics? Selecting the appropriate sensors, data analytics tools, and machine learning algorithms is crucial.
These technologies should seamlessly integrate with your existing infrastructure, allowing for real-time monitoring and analysis of equipment performance.
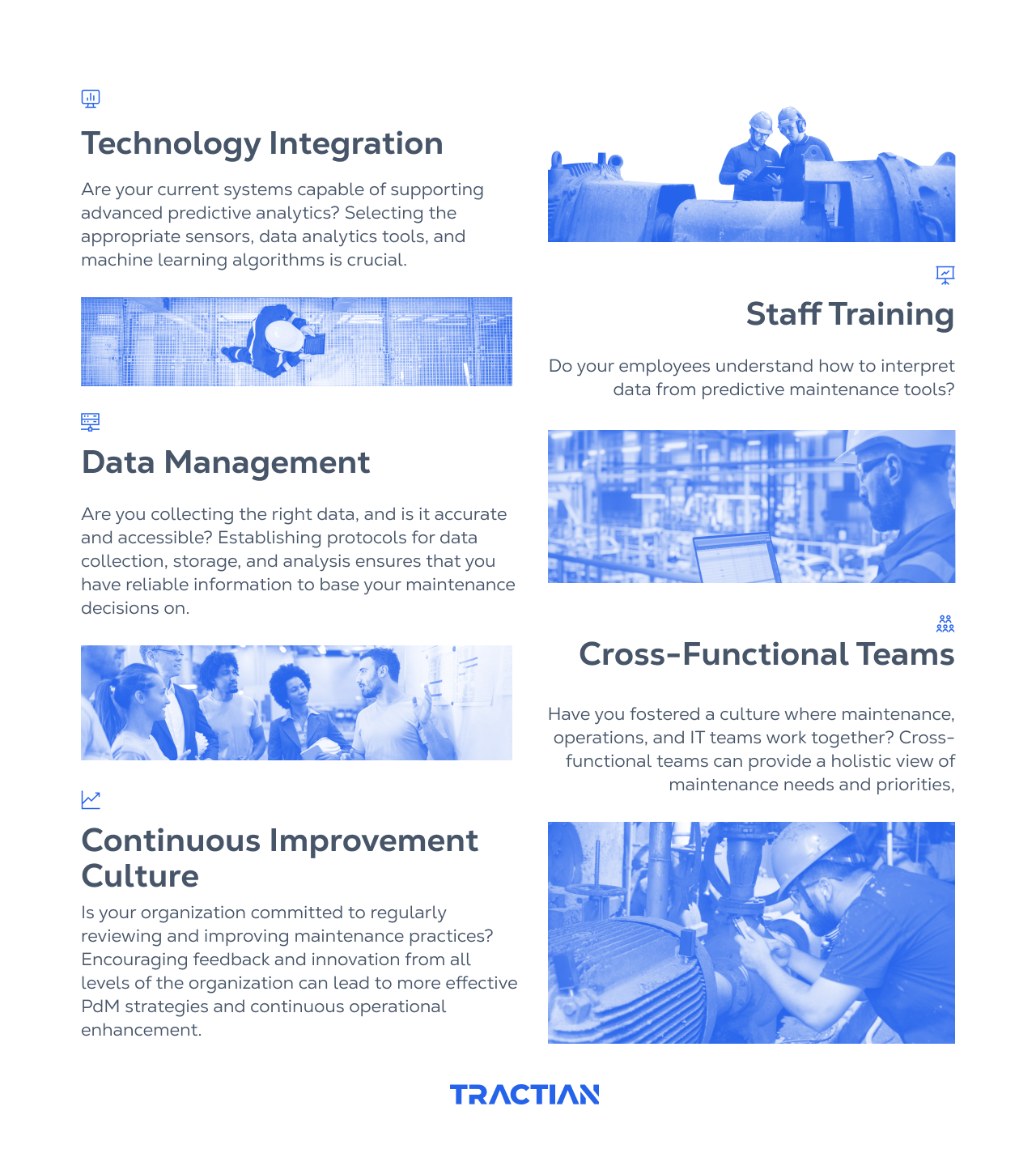
Technologies Driving Predictive Maintenance in the Food Sector
The food industry’s shift toward PdM practices is powered by several key technologies, each playing a pivotal role in streamlining operations and enhancing production efficiency.
Let’s take a closer look at some of them:
IoT and AI-assisted Sensors
The Internet of Things (IoT) and artificial intelligence (AI) are at the forefront, with smart sensors collecting data from machinery, enabling real-time monitoring and analysis.
For example, wireless sensors can detect the different scales of machinery vibration, identifying potential issues before they escalate into failures.
Companies like TRACTIAN use AI and ML to recognize thousands of industrial machinery vibrations, helping to predict maintenance needs.
CMMS and EAM Software
Computerized Maintenance Management Systems (CMMS) and Enterprise Asset Management (EAM) software are crucial for managing and analyzing the vast amounts of data generated by sensors.
They provide a centralized platform for tracking maintenance activities and analyzing trends, facilitating more informed decision-making.
Machine Learning and Data Analytics Platforms
These technologies process and analyze the sensor data, identifying patterns and predicting potential equipment failures.
Advanced analytics tools, including machine learning, enable real-time prediction of failures, helping to optimize maintenance schedules and prevent downtime.
Augmented Reality and Virtual Collaboration Tools
Augmented reality (AR) can significantly enhance operator training and maintenance procedures, allowing for virtual collaboration and improved uptime.
AR tools help visualize machine health and assist in diagnosing issues, enabling timely and effective maintenance actions.
Navigating the Challenges of PdM Adoption in the Food Industry
Nobody said it would be easy, right? Adopting a PdM approach in the food industry comes with its set of challenges.
How can these be effectively managed? We’ll draw you a simplified map, take a look:
Data Complexity
The overwhelming amount of data from various sources can be daunting.
To navigate this, food manufacturers should invest in robust data management systems and analytics tools that can integrate and simplify data interpretation, making actionable insights more accessible.
For example: start by identifying the most critical data points for maintenance decisions and focus on integrating these into your analytics platform first.
Skill Gaps
The technical nature of predictive maintenance might highlight a skills gap in existing teams. Address this by providing targeted training and upskilling programs to ensure staff can effectively use new technologies and interpret the data they produce.
Check this tip: create a mentorship program where experienced staff can guide less experienced team members through the nuances of PdM technologies and data analysis techniques.
Initial Investment Costs
The upfront costs for technology and training can be significant.
Manufacturers should consider phased implementations, starting with critical areas to demonstrate value and gain buy-in. Exploring financing options or partnerships with technology providers can also alleviate financial pressures.
Here, try and negotiate with technology providers for trial periods or phased payment plans that align with the success milestones of the pilot program.
Future-Proofing Food Manufacturing: The Next Wave in Predictive Maintenance
As we look to the future of food manufacturing, predictive maintenance is set to evolve with the rapid advancement of Industry 4.0 technologies.
So, how will this shape the next wave of maintenance practices?
Emerging trends point towards deeper integration of AI and robotics, with smart factories employing autonomous robots for maintenance tasks, driven by AI’s predictive insights.
Imagine robots conducting inspections and repairs in areas hazardous to humans, or AI algorithms optimizing maintenance schedules in real-time based on production demands and machine health.
Moreover, the integration of digital twins—virtual replicas of physical assets—will enable more accurate simulations and testing of maintenance strategies before implementation.
This could dramatically reduce downtime and improve efficiency.
The ongoing advancements in AI and machine learning are expected to make PdM more intuitive, less resource-intensive, and even more reliable.
Embracing Predictive Maintenance: Key to Future-Ready Food Industry Operations
We know: at the ground level, PdM is just another maintenance strategy. But the reality shows something different (and bigger): a pivotal component in the food industry’s journey toward operational excellence.
By enabling proactive maintenance, it significantly reduces unplanned downtime, boosts production efficiency, and upholds the stringent standards of food safety, thereby driving profitability.
Answer us: Isn’t it time for stakeholders in the food industry to view predictive maintenance as a strategic investment that ensures future readiness and competitive advantage, rather than merely a cost center?
Embracing this approach means committing to technological innovation and continuous improvement, ensuring that operations remain resilient against the challenges of tomorrow.
With PdM at the core, the food industry can achieve operational efficiency, sustainability and growth.
Are you prepared to invest in the future of your food industry operations?