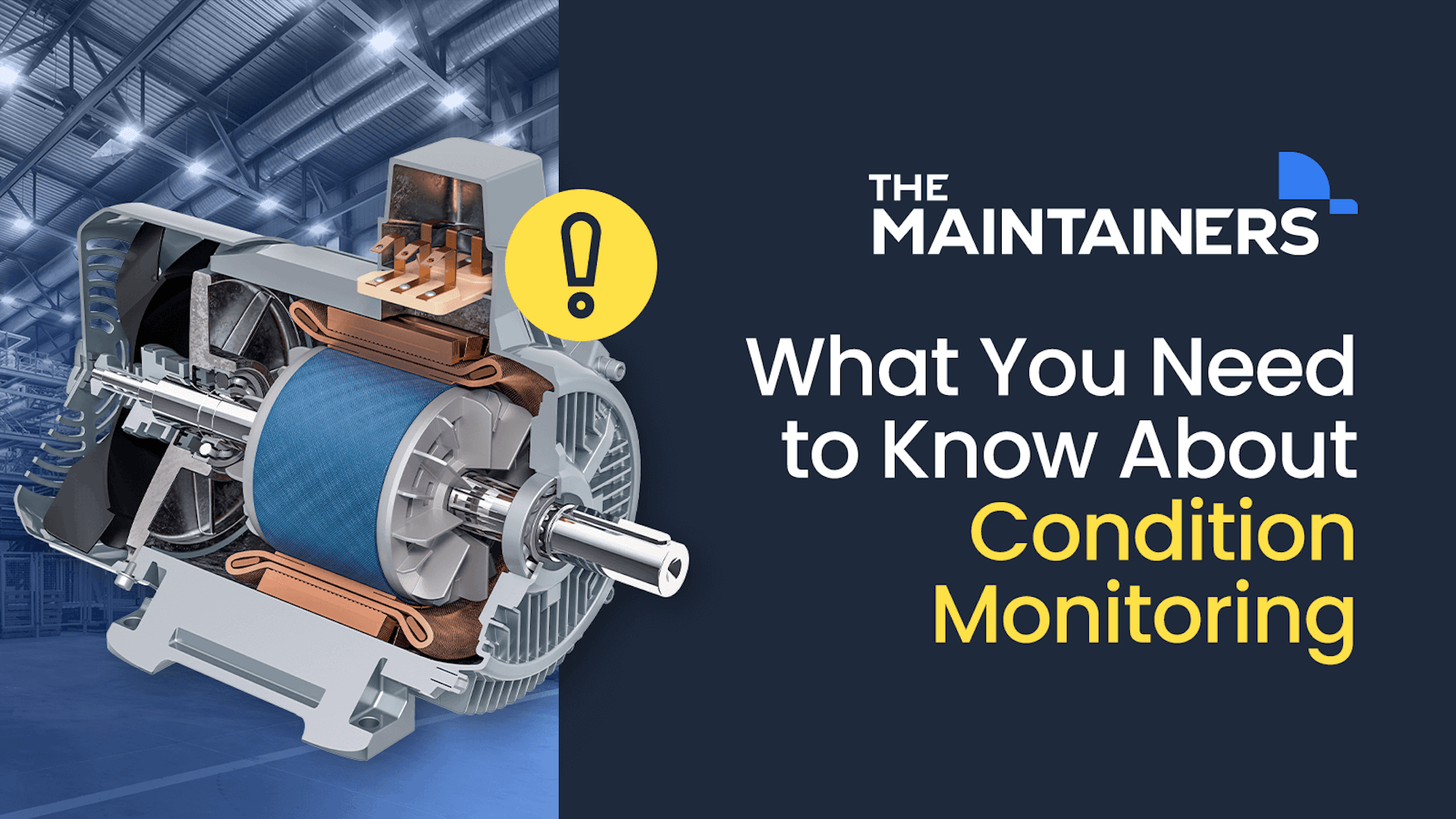
The Complete Guide to Condition Monitoring
By The Maintainers • May 08, 2023
In the maintenance industry, all of production depends on assets being able to operate. That being said, many workers are still running into the same common problem: having no way to tell when assets are going to fail, or when they need replacement.
What we do know is that asset failures don’t just happen – there’s always a series of events leading up to downtime. It’s all about tracking that series of events from the beginning, hopefully giving you the ability to control the outcome.
Much like monitoring a cough or fever in humans, condition monitoring analyzes assets, collecting data about each machine and relaying it back to maintenance and reliability teams. It’s done to help predict unknown failures, bringing maintainers closer to zero unplanned downtime.
What Is Condition Monitoring?
Condition monitoring, a type of industrial maintenance also known as condition-based monitoring, condition-based maintenance, or CbM, is a form of proactive asset monitoring that’s useful in many different sectors of industrial maintenance. Used instead of corrective or reactive maintenance, CbM uses different testing methods and techniques to predict failures before they happen.
Its job is simple: to assess machine condition and give teams the information needed to create the most optimized maintenance strategy possible. Using this approach, the goal is to avoid machine failures and unplanned downtime, in turn increasing productivity and profitability.
Types of Condition Monitoring
There are four condition monitoring techniques commonly used today:
- Acoustic emission has to do with asset sounds. We can monitor the sounds each machine emits, letting us detect any changes happening in the high-frequency emissions early on. This type of monitoring is commonly used for equipment with roller bearings, those that could have a lack of lubrication, and those that could have bad seals.
- Thermography is all about the temperature of an asset. Moving parts create heat; this technique identifies, monitors, and registers changes in component temperature levels, catching overworked assets before they lead to a fault or failure. A thermal image, or thermogram, is then generated, helping teams avoid overheating.
- Oil Analysis provides accurate information about the condition of a machine and its lubricant. It detects contamination, gear failures, oxidation, misalignment, additive depreciation, and wear of mechanical components, letting teams know before a machine failure happens. You can monitor contaminated oil as well as the wear of metals and additives in the oil; this helps teams define a better changeover time.
- Vibration Analysis is the most common and accurate type of condition monitoring. It analyzes a machine’s vibration pattern, giving maintainers an easy way to detect gear wear, mass unbalance, shaft misalignment, and warping, among others. Commonly used in machines with rotating pieces, bearings that sustain wear, and assets that can leak, vibration analysis helps maintenance teams avoid future failures and unplanned downtime.
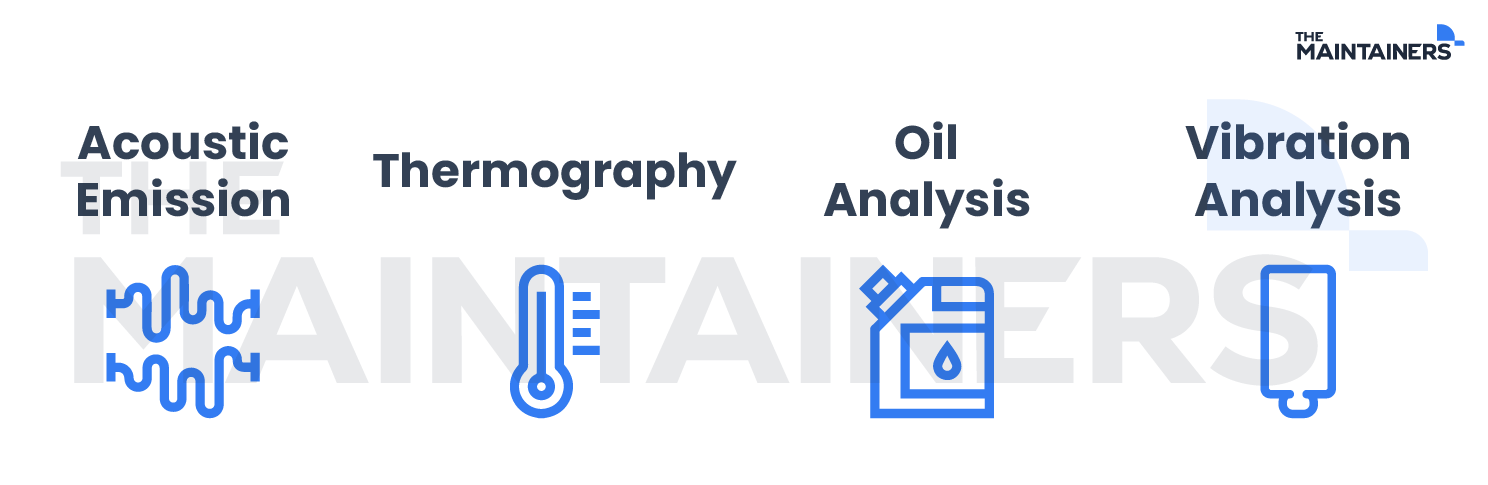
All of these types of condition monitoring can and will work together, all it takes is the common goal of wanting to optimize the companies’ industrial maintenance strategies.
When Should You Use Condition Monitoring?
Of course, to monitor an asset there must be something that can be detected – objects without measurable parameters cannot use condition monitoring.
With this in mind, CbM can be applied to almost any asset. It tends to work best for machines that are constantly operating, and those that are most critical to worker safety and production line operation.
Specifically, teams commonly use condition monitoring on these assets:
- Assets that are sensitive to extreme temperature
- Assets and environments that are sensitive to high pressures
- Assets that rely on oil or lubrication for operation
As companies increase their size, their maintenance strategies should follow suit. This type of monitoring makes it easy to monitor a large number of assets at once, giving back time to the maintainers.
Condition monitoring should be used by maintenance and reliability teams that are growing, want to stay informed about their assets, reduce unplanned downtime, and create proactive maintenance strategies.
Potential Barriers to Entry of Condition Monitoring
Before we get into the many reasons condition monitoring can add value to your maintenance strategy, let’s go over some of the potential barriers to entry.
As with almost any maintenance strategy, the initial implementation of condition monitoring sensors and asset monitoring and management software will cost you. But, because of how proactive strategies work, condition monitoring ends up saving you money – helping you avoid costly downtime.
Training the maintenance team on condition monitoring systems is necessary, no matter how simple. Each maintainer will benefit from understanding how the system works, in turn helping the team reach their goal.
Implementing new maintenance plans can be unpredictable, just like failures. It’s important to build a team that can change gears quickly to do what’s best for the company.
Benefits of Condition Monitoring
Now we can shift gears and get into the benefits of condition monitoring – and there are many.
- Higher productivity
- Assets are only productive when they’re operating.
- Assets are only productive when they’re operating.
- Increased reliability
- Monitoring assets 24/7 means less chance of failure.
- Monitoring assets 24/7 means less chance of failure.
- Decreased downtime
- Predicting failures before they happen means less downtime.
- Predicting failures before they happen means less downtime.
- Reduced maintenance costs
- With less unplanned repairs and maintenance there are less surprise costs.
- With less unplanned repairs and maintenance there are less surprise costs.
- Create planned downtime
- By monitoring an assets’ condition you can create a work order or schedule for repairs and maintenance to follow.
- By monitoring an assets’ condition you can create a work order or schedule for repairs and maintenance to follow.
- Improved worker safety
- If maintainers can plan for maintenance, there’s less chance for something to go awry.
- If maintainers can plan for maintenance, there’s less chance for something to go awry.
- Longer asset lifespan
- When you stop putting your assets through multiple large repairs and plan for regular maintenance, you can extend their lifespan by multiple years.
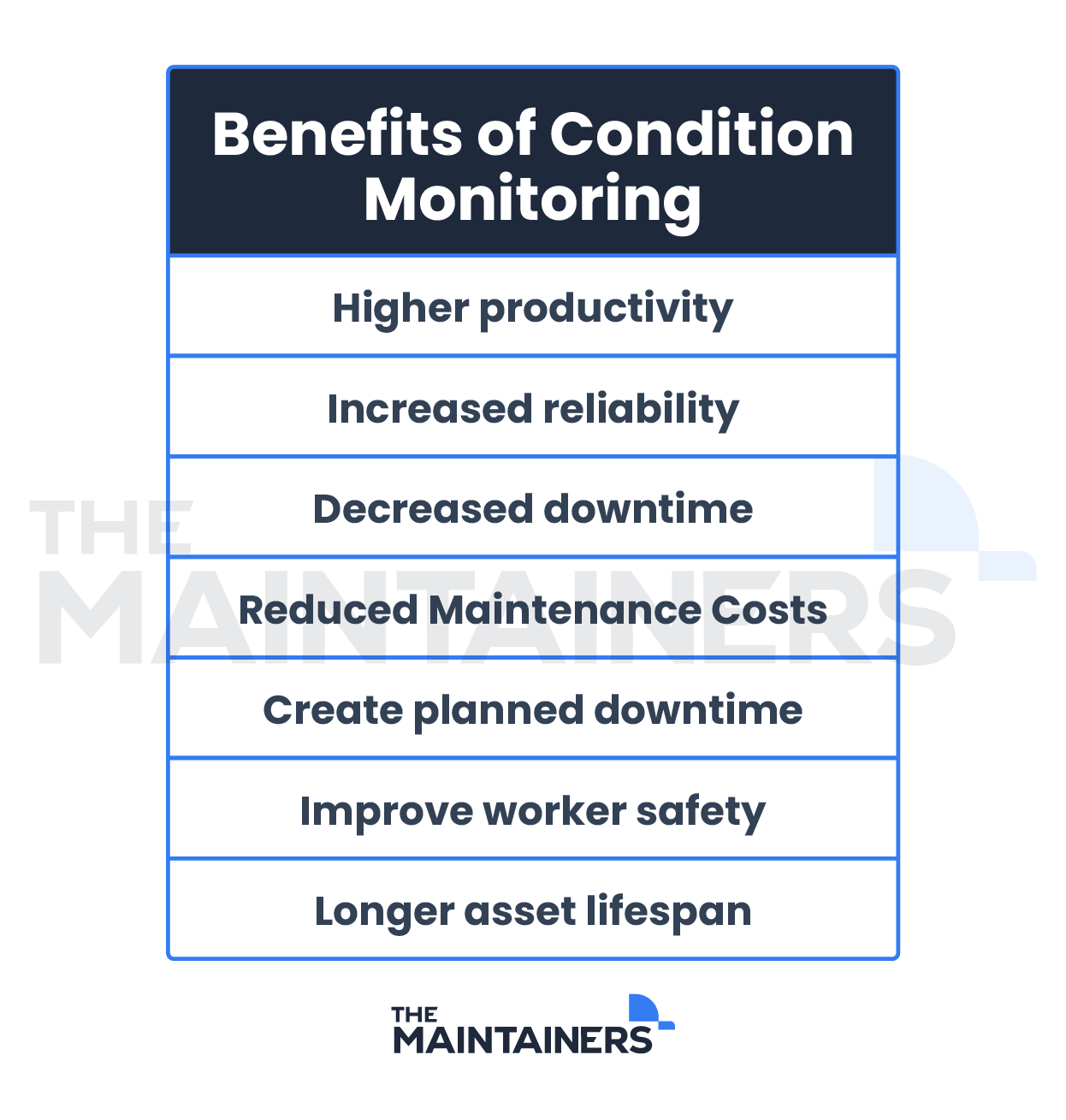
How Does Condition Monitoring Work?
Condition monitoring, at its simplest, is just a way to monitor the condition of an asset in real time. It uses the four techniques laid out above to collect data from machines, giving maintenance teams a chance to analyze that data and predict machine faults and failures.
Using its techniques and pillars, maintenance teams can monitor the condition of their most critical assets, giving them an insight into the machine’s current health. What you don’t know, you can’t plan for, so maintainers use condition monitoring to predict and prevent negative issues with their assets.
Implementing Condition Monitoring
To implement condition monitoring, there are just a few steps you need to take.
The most common way to implement condition monitoring on your shop floor is by finding a sensor with a CMMS or asset management platform. Each asset will have a sensor attached – this is what relays data back to the platform.
Using the software and sensor together allows you to monitor each asset for vibration, acoustic emission, oil quality, and temperature. Once the sensors and software have been implemented, you’ll monitor each asset using the four pillars:
- Detection covers when the fault happened, how long it took to be noticed, and how long until complete failure.
- Diagnosis details what the issue is, its origin, its severity, and how quickly it’s growing.
- Prognosis explains the fault severity, giving you a forecast of its side effects and aftereffects.
- Programme is the step where you create the repair or maintenance schedule and timeline of operation.
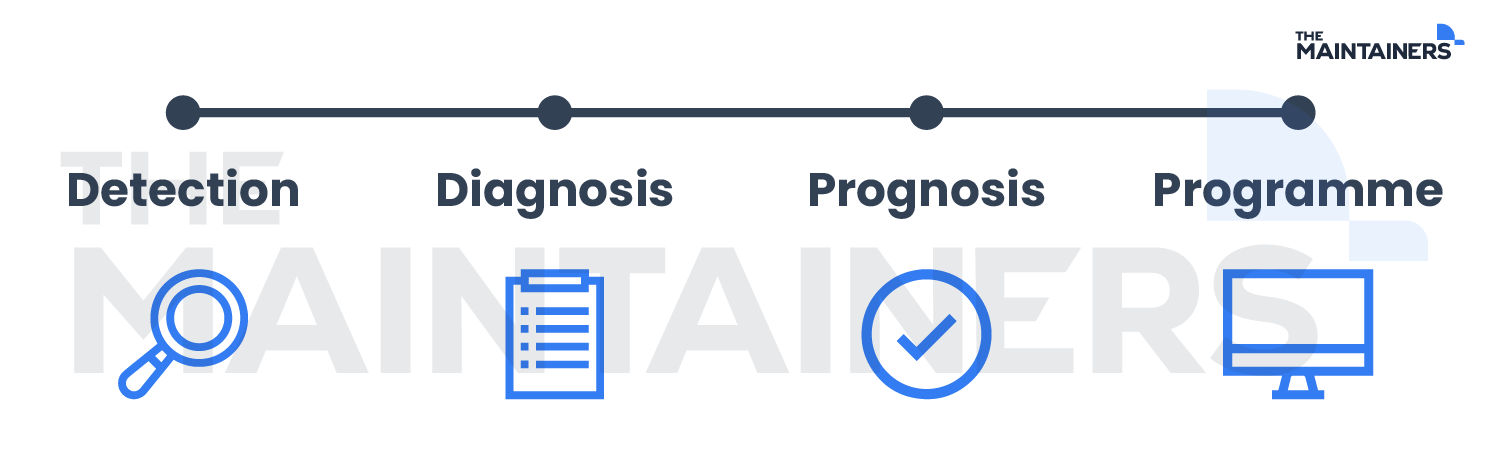
Why Is Condition Monitoring Important?
Condition monitoring is a crucial machine maintenance strategy for every single company in the industry.
First, it’s about the Maintainers – CbM helps find and address pain points they’ve recognized in day to day operations. Armed with this information, they can make informed decisions about machine maintenance in their company.
Condition monitoring isn’t only useful for Maintainers; companies often use it to collect and analyze data necessary to improve machine reliability, long-term asset health, and to continue optimizing their own maintenance procedures.
Any way you look at it, condition monitoring is a tool needed to optimize maintenance strategies in the industry.