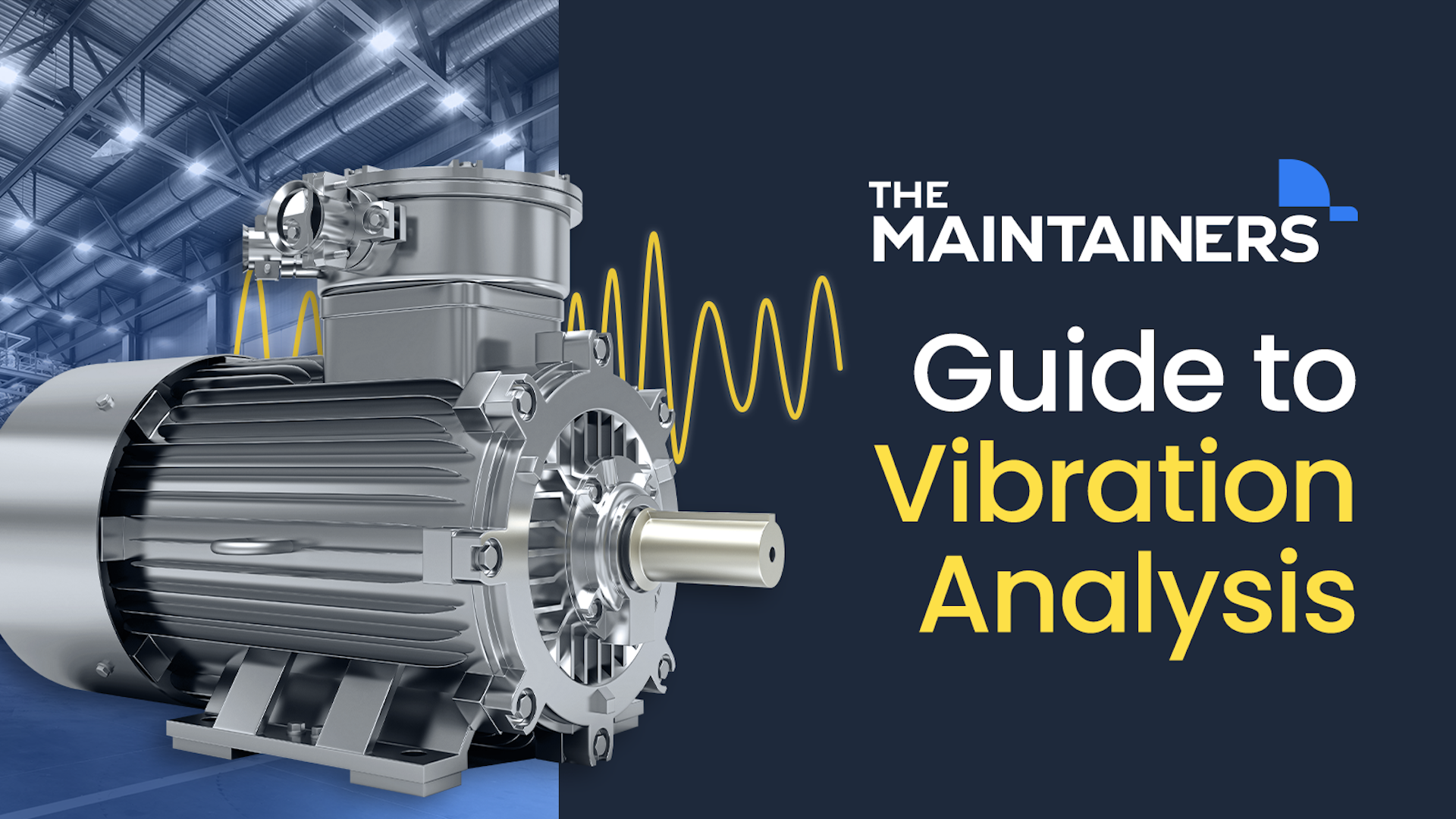
Everything You Need to Know About Vibration Analysis
By The Maintainers • June 05, 2023
Our world is filled with machines and structures, and ensuring their smooth operation is essential. But, have you ever wondered how experts monitor and understand the movement of these systems?
Vibration analysis is the most popular and common way to monitor asset condition. It helps us understand the insights behind vibrations produced by different objects. No matter the object, analyzing vibrations gives us a deeper understanding of their health, performance, and potential risks.
In order to fully understand vibration analysis, we must first learn the basics.
What Is Vibration Analysis?
Vibration analysis is a scientific method used to study and understand the behavior of vibrations in objects or systems. In maintenance, it’s the measuring, analyzing, and interpreting of vibrational patterns, frequencies, and characteristics produced by machinery.
These vibrations give maintenance workers insights into the condition, performance, and potential problems of the asset.
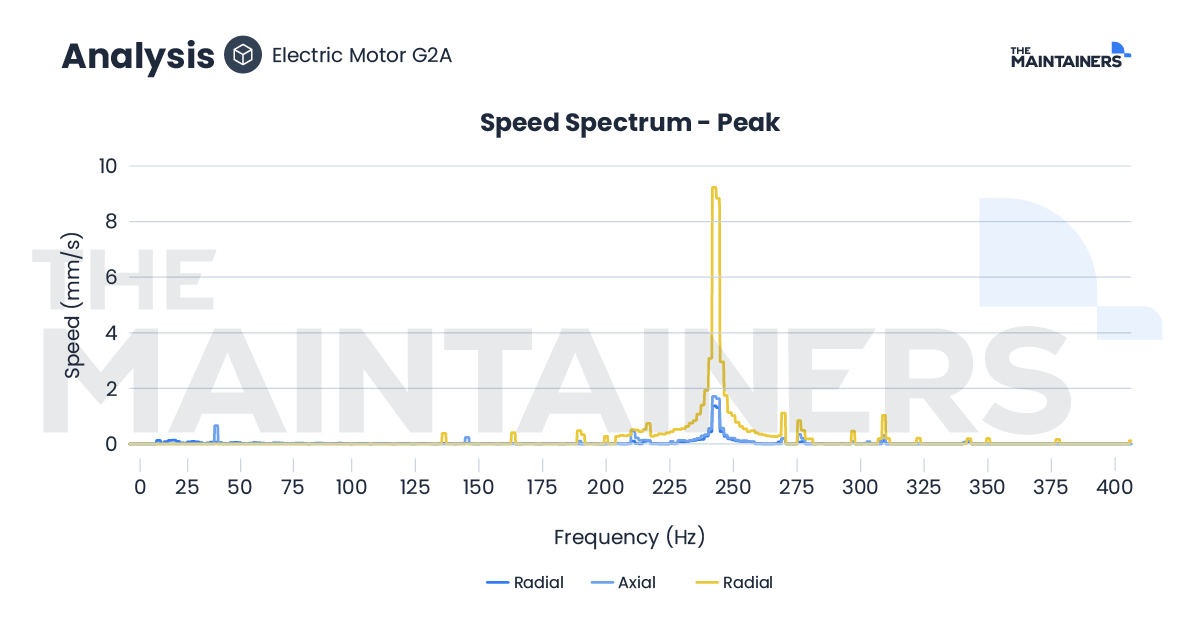
What Is Vibration Analysis Used For?
The safety and reliability of various assets relies on vibration analysis. It detects faults, identifies sources of vibration, and enables timely maintenance and corrective measures. Other reasons it’s used include:
- Machine Health Checks: Analyzing the vibration of rotating machines keeps you up to date on their condition.
- Preventive Maintenance: Regular machine check-ups help catch potential issues before they cause problems.
- Finding Machine Faults: Vibration analysis helps identify the root cause of failure in machines.
- Assessing Performance: Machine performance can be evaluated through its vibration patterns.
- Ensuring Quality: Product quality can be guaranteed through the use of vibration analysis.
- Checking Structures: The strength of buildings, bridges, and other structures can be assessed using vibration analysis.
How Does Vibration Analysis Work?
In order to measure machine vibrations, collect data, and analyze it, the vibration analysis process must follow these steps:
- Collect Data: Sensors gather information about the vibrations coming from the monitored machine.
- Take Measurements: The sensors detect the vibrations and convert them into electrical signals. These signals are then measured.
- Process the Data: To organize and analyze it effectively, the measured data is processed using digital signal processing.
- Analyze Frequencies: Frequency analysis involves transforming the collected vibration data from the time domain to the frequency domain. This is done using methods like Fourier analysis, which helps identify different vibration patterns.
- Recognize Patterns: To identify normal and abnormal patterns of vibration, compare the collected data with historical information. This helps determine which vibrations are within expected levels, and which indicate potential problems.
- Identify Faults: Once faults are identified, further analysis is done to determine their possible causes.
- Report and Start Maintenance: After the fault diagnosis is complete, a detailed report summarizing the findings is generated. This report can be used as a basis for a maintenance plan.
Let’s say “Motor X” is the asset being analyzed.
MOTOR X
- Number of Poles: 4
- 60Hz rotation: 3600 RPM
- Gear A: 36 teeth / Gear B: 72 teeth
- Max temperature: 140 ºF
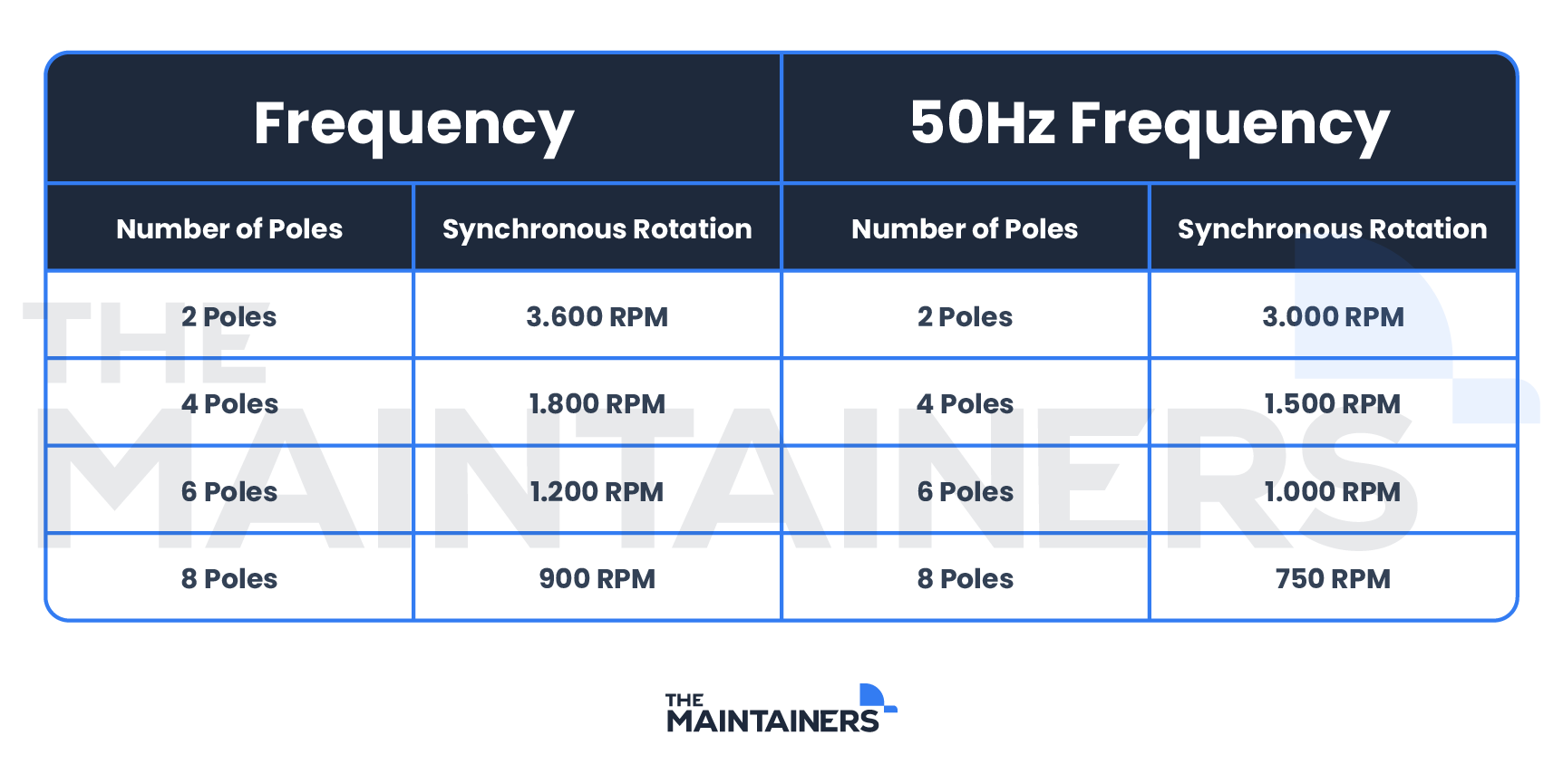
By analyzing its vibrations, we start to see patterns in the vibration diagrams. The goal is to build a base graph – it will help identify variations that characterize possible issues.
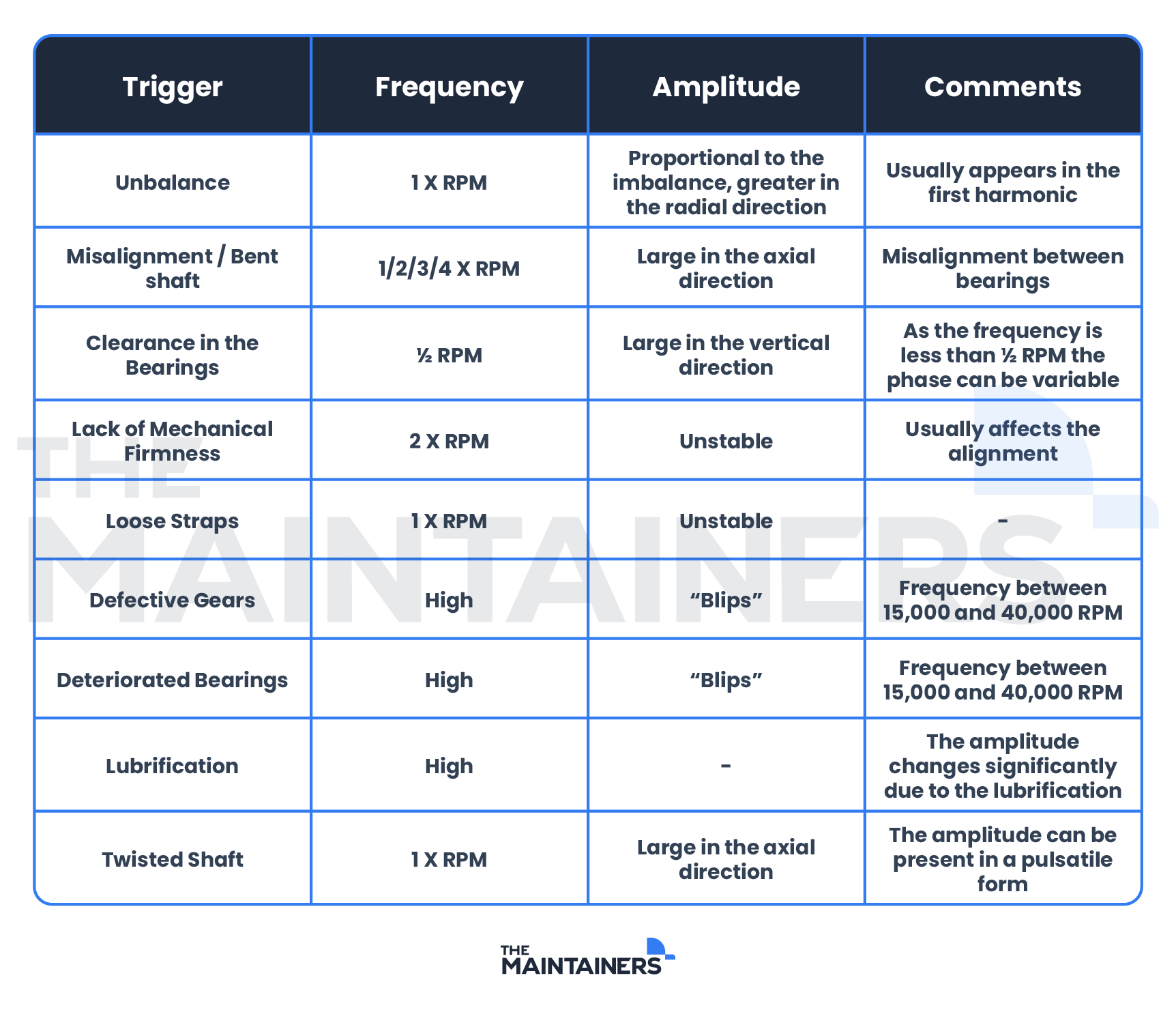
Above, you can see how changes in Motor X’s vibration patterns can be used to detect possible faults or failures. Not only is the trigger shown, but also the frequency and amplitude that caused it.
Types of Vibration
Several types of vibrations are commonly observed and analyzed in the industry, including:
- Free or Natural Vibrations happen when a system or component vibrates without any external force applied.
- Forced Vibration occurs when a system or component is subjected to an external force or excitation.
- Resonance happens when the frequency of an external excitation matches the natural frequency of a system or component.
- Torsional Vibration refers to vibrations that occur along the rotational axis of a shaft or rotating component.
- Lateral Vibrations involve side-to-side or transverse movements of a machine or structure.
- Axial Vibrations happen along the axial direction of a machine or component, parallel to the rotation or motion.
- Structural Vibrations are vibrations that affect the entire structure of a machine.
Types of Vibration Analysis
Before learning the tools that help us measure vibration waves, we must first learn how to obtain vibration spectrums. They can be collected in three ways:
Global level vibration meter without filter: These are instruments that can measure the global value of vibration over a wide frequency.
Global level vibration meter with filter: The same as without filter, but they measure vibration levels of the most critical assets.
Frequency analyzers: These are used in cases where the width of the filter is very narrow. Frequency analyzers can perform the Fourier Transform on a random, periodic or transient signal.
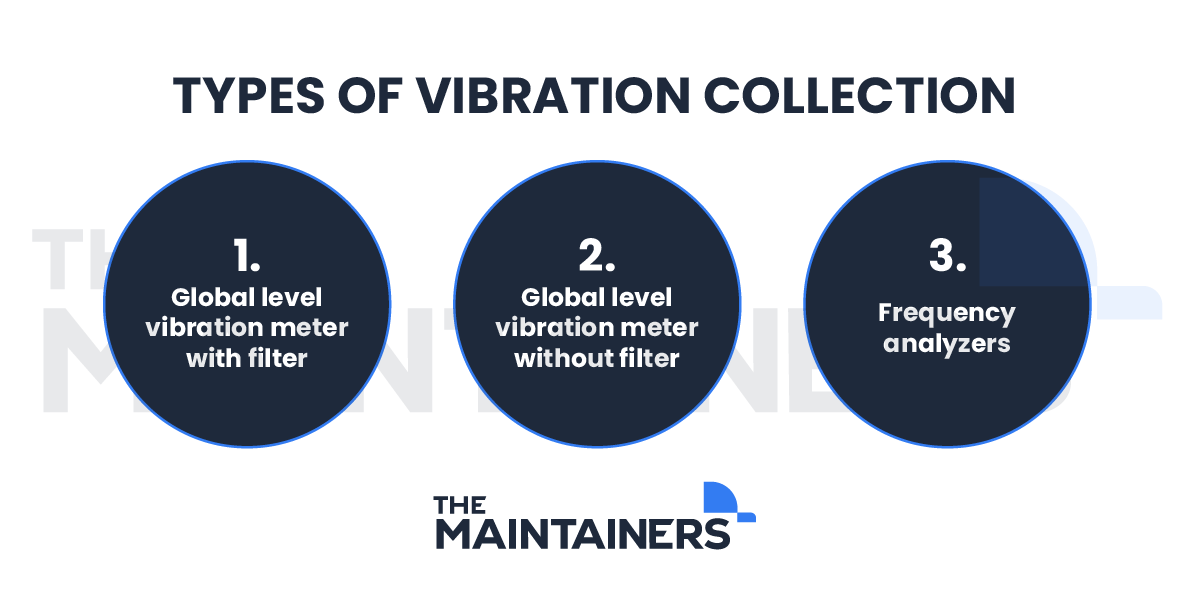
How to Measure Vibration
The next step is choosing the right tool for your specific project. This will depend on the type of machine or structure you’re analyzing. Below are a few of the most commonly used vibration analysis tools and sensors:
Accelerometers detect and measure acceleration, which is then used to calculate vibration parameters. They’re attached to the surface of the machine and can measure vibrations in different directions (typically the triaxial type). They convert the mechanical vibrations into electrical signals that can be recorded and analyzed.
Proximity Probes are commonly used to measure displacement or position changes in rotating machinery. They’re placed close to the rotating part and measure the gap or displacement between the probe and the rotating element. By analyzing the changes in the gap, vibrations can be determined.
Laser Vibrometers use laser beams to measure vibrations without physical contact with the object. The beam is directed towards the surface, and the reflection is analyzed to determine the velocity or displacement of the surface. Laser vibrometers are particularly useful for measuring vibrations on delicate or hard to access surfaces.
Strain Gauges are sensors that measure changes in strain or deformation in a material. They measure vibrations indirectly by detecting the resulting strain caused by vibrations.
Tachometers are instruments used to measure the rotational speed or frequency of rotating machinery. By measuring the rotational speed, vibrations associated with unbalance or misalignment can be estimated. Tachometers often use optical or magnetic sensors to detect the rotational motion.
Data Loggers are devices that can record and store vibration data over time. They are often used in conjunction with accelerometers or other sensors to constantly monitor and capture vibration measurements. Data loggers can be programmed to record data at specific intervals or triggered by certain events.
Spectral Analyzers are instruments or software tools used to analyze the frequency content of vibration signals. They take the recorded vibration data and perform a frequency analysis, revealing the dominant frequencies and their amplitudes. This analysis helps identify specific frequencies associated with faults or abnormal conditions.
It’s important to note that different measurement methods may be suitable for different situations and types of vibrations. It depends on the nature of the vibration, access of the measurement point, accuracy requirements, and the specific equipment being monitored.
Benefits of Vibration Analysis
There are several benefits of vibration analysis across various industries and applications. Some of its key advantages include:
- Early Fault Detection: Vibration analysis can detect potential faults in machines, equipment, or structures at an early stage.
- Condition Monitoring: Vibration analysis provides continuous monitoring of machinery and equipment, allowing for real-time assessment of their operating conditions.
- Improved Equipment Reliability: By identifying and addressing underlying issues, the reliability of machinery and equipment can be significantly improved.
- Cost Savings: Implementing vibration analysis as part of a predictive maintenance program can lead to cost savings.
- Extended Equipment Lifespan: Vibration analysis allows us to detect and correct problems that contribute to premature equipment wear and failure.
- Enhanced Safety: Vibration analysis aids in ensuring the safety of personnel working with or around machinery.
- Increased Energy Efficiency: Vibration analysis can uncover defects in machinery and equipment that lead to excessive energy consumption.
- Data-Driven Decision Making: Vibration analysis generates data that is analyzed to make informed decisions about maintenance strategies and process optimization.
Using this type of analysis, maintenance and reliability teams can keep machinery and equipment safe and efficient. These important insights can be used to make informed decisions and improve operations, leading to greater productivity and performance.
Vibration analysis programs can help you find and fix problems before they become expensive failures. This proactively reduces downtime and extends equipment life.
Start using vibration analysis today to make informed choices and optimize your operations for success.