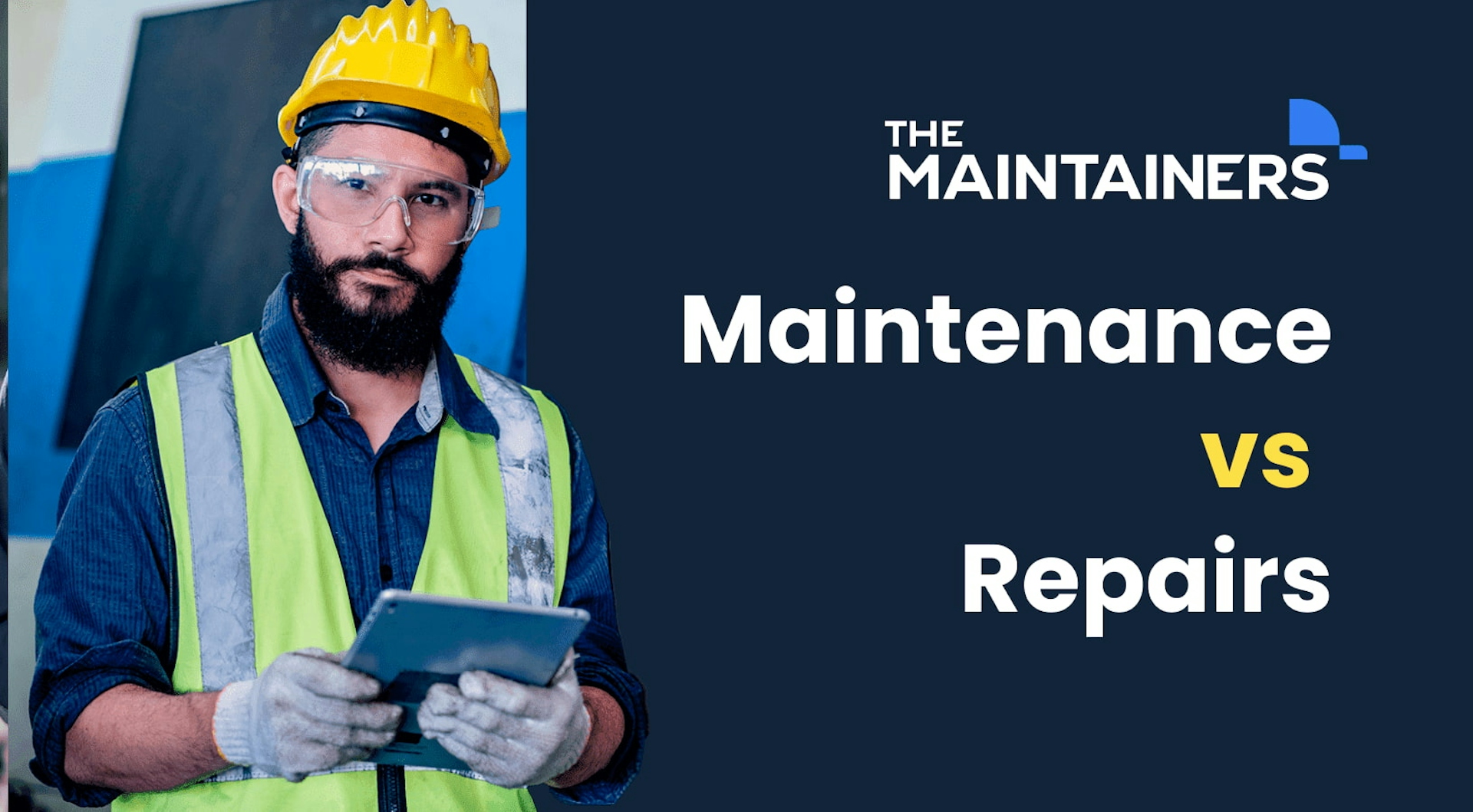
Navigating the Fine Line Between Maintenance and Repairs
By The Maintainers • October 19, 2023
In the world of manufacturing, understanding the nuanced difference between maintenance and repairs is important for seamless operations. Knowing the difference between the two seemingly similar terms can make all the difference in effective asset management, cost control, and operational efficiency in any industry. It enables organizations to adopt a proactive approach to maintenance, which ultimately contributes to smoother operations and higher productivity.
Repairs and Maintenance: What’s the difference?
Concisely, maintenance refers to the preservation and protection of an industrial asset’s integrity and performance. This includes routine checks, adjustments, and necessary replacements, all aimed at preventing potential issues.
Repairs, in contrast, are reactive measures taken in response to specific issues or malfunctions. They are conducted to rectify existing problems and restore functionality.
Basically, maintenance prevents problems from occurring, while repairs aim to solve the problem after it has happened. Balancing maintenance and repairs is critical in the manufacturing setting, with effective strategies to ensure optimal operational efficiency while minimizing unplanned downtime.
Types of Maintenance
There are several different types of maintenance that teams can implement, and finding the appropriate strategy is dependent on the company’s context and specific needs.Thoroughly understanding their critical assets and how they function can help a team develop the ideal maintenance practice to optimize reliability, availability, and profitability.
Maintenance falls into two broad categories:
Risk-Based Maintenance (RBM) – a proactive maintenance strategy that prioritizes maintenance activities based on the level of risk associated with each asset or system. This approach aims to optimize the allocation of resources by focusing efforts on high-risk areas, where failure could have significant consequences in terms of safety, environmental impact, or financial loss. Corrective and reactive maintenance fall under this category.
Reliability Centered Maintenance (RCM) – a systematic approach to maintenance planning and decision-making aimed at optimizing the reliability, safety, and cost-effectiveness of physical assets within an organization, and sets safe minimum levels of asset upkeep. It involves identifying the most appropriate and efficient maintenance strategies for each component or system based on its criticality and impact on operations. Preventive, predictive, and proactive maintenance strategies fall under this category.
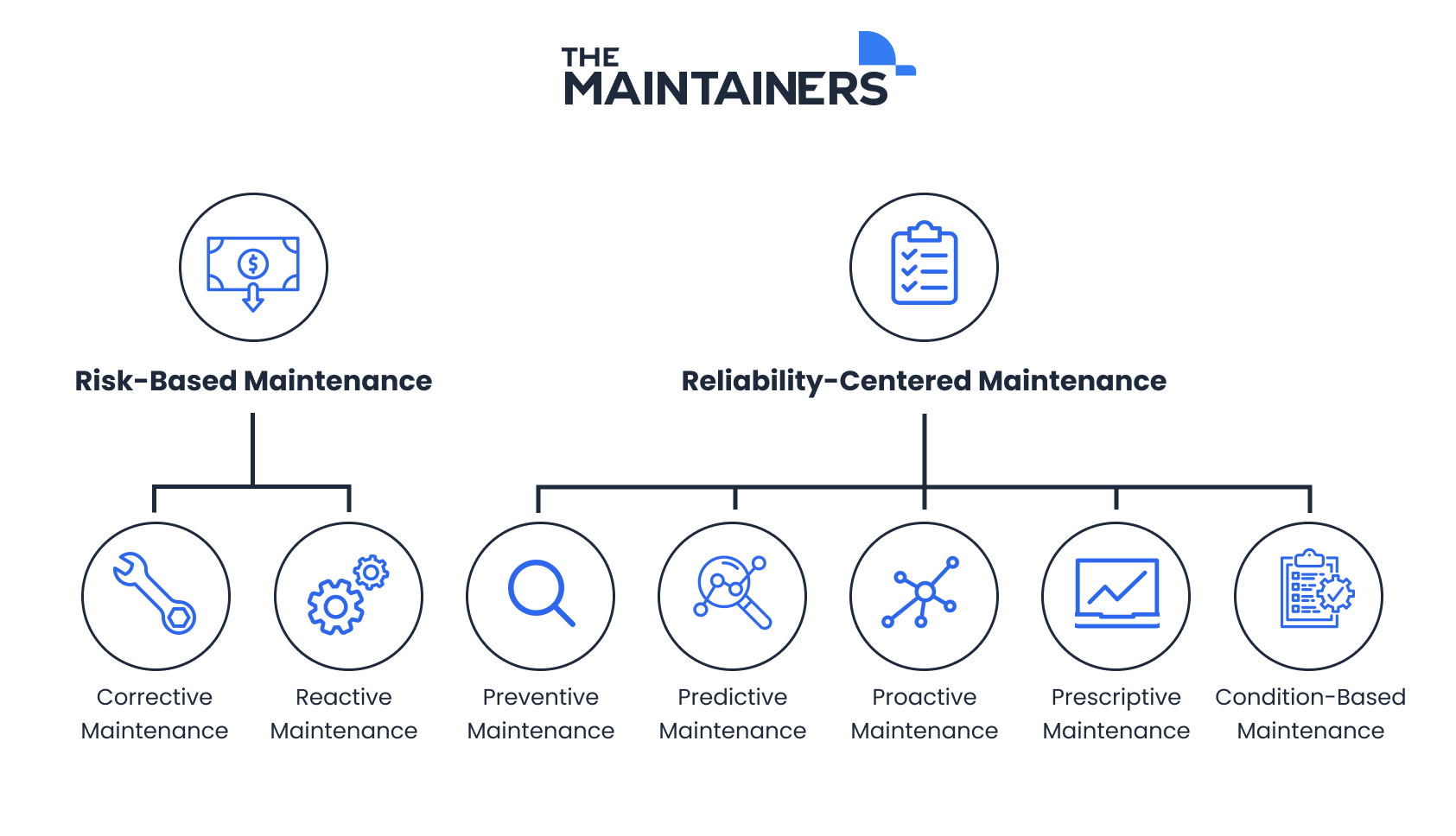
Types of Repairs
As mentioned above, repairs are tasks undertaken to fix or mend a component or asset, and usually occurs before, during, or after failure.
There are two types of failure that repairs aim to fix: partial and total.
Partial failure occurs when a system or component does not perform its intended function at a reduced capacity or efficiency, but it still maintains some level of functionality. For example, in an electrical system, a partial failure may involve a component like a transformer operating at a reduced capacity, leading to voltage fluctuations but still allowing the system to function to some extent.
Total failure, on the other hand, occurs when a system or component ceases to perform its intended function completely. It is unable to operate as designed and may be non-functional. It is characterized by complete operational shutdown, no output, and almost always immediate action required.
While partial failures are less significant than total failures as issues like degradation and wear are often more easily eliminated and resolved compared to complete loss of functionality, it is important to know that issues regarding partial failures can be harder to detect than total failures, as the asset still maintains functionality.
In this sense, we can re-emphasize the difference between maintenance and repair: repairs restore asset functionality after downtime to minimize loss, and maintenance preserves functionality to prevent unplanned downtime.
Repairs or Maintenance: Which is more cost-effective for my company?
Historically, repairs have always been more expensive than maintenance strategies, especially in the long-term. Both strategies have multiple advantages and disadvantages.
Repairs
Advantages:
- Immediate Fix: Repairing an asset can provide a quick solution to an existing problem or failure, restarting production right away.
- Lower Upfront Cost: In some cases, the immediate cost of a repair may be lower compared to implementing comprehensive maintenance practices.
Disadvantages:
- Potential for Recurrence: If the root cause of the issue is not addressed, there is a risk of the problem recurring, leading to additional repair costs.
- Downtime Costs: Depending on the criticality of the asset, downtime during repairs can result in significant production or operational losses.
Maintenance
Advantages:
- Extended Asset Lifespan: Regular maintenance can extend the lifespan of assets, reducing the frequency of replacements.
- Lower Total Cost of Ownership (TCO): While upfront maintenance costs may be higher, the overall TCO of an asset is often lower when good maintenance practices are implemented.
Disadvantages:
- Upfront Investment: Implementing a robust maintenance program may require an initial investment in training, tools, and systems.
- Ongoing Commitment: Maintaining assets over time requires a consistent commitment of time, resources, and personnel.
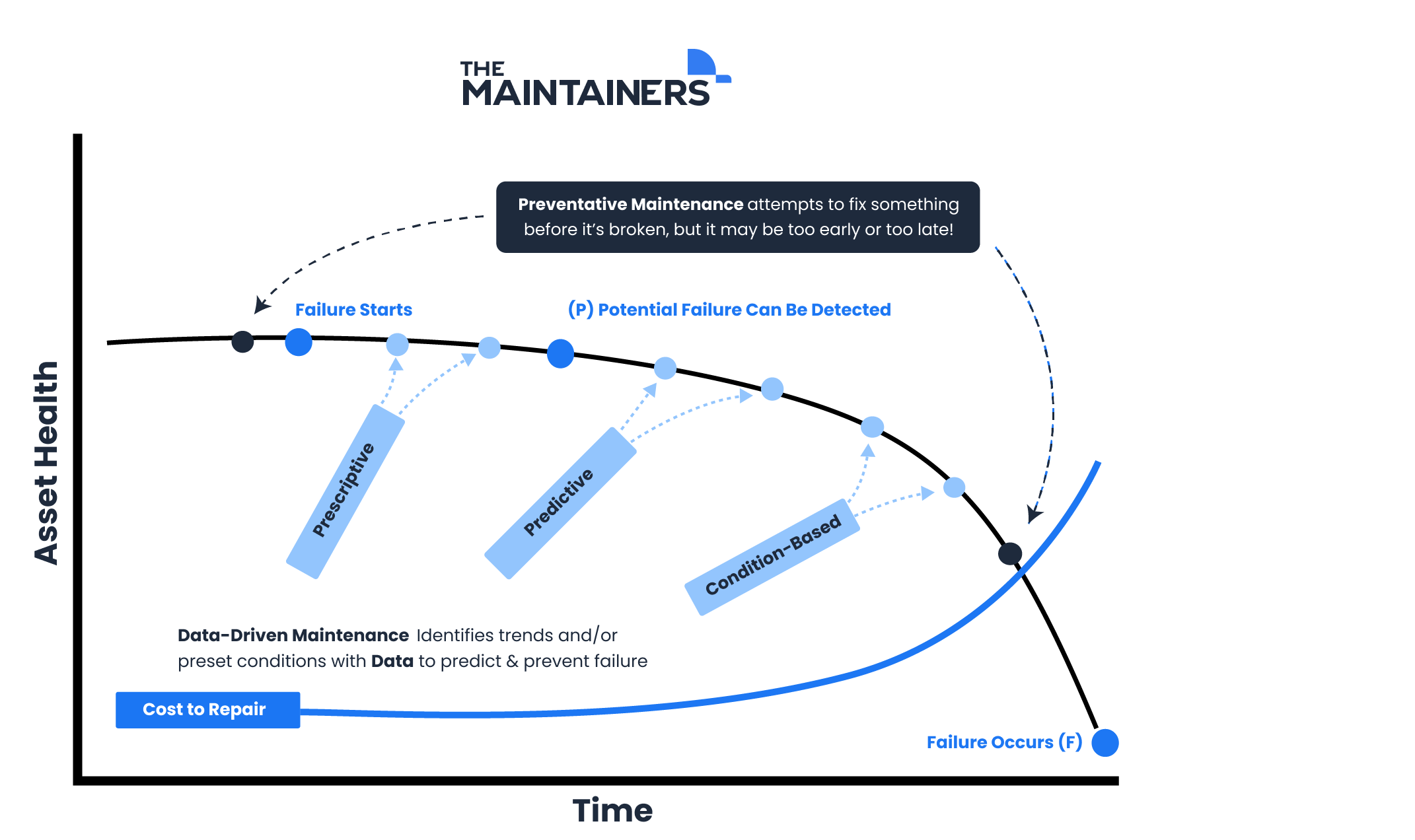
In the long run, implementing good maintenance practices is generally more cost-effective for critical assets and systems. While it may involve higher upfront costs, the benefits in terms of extended asset lifespan, reduced downtime, and improved reliability often outweigh the initial investment.
It’s important to note that a balanced approach is optimal. This involves addressing immediate repairs when necessary while also incorporating the right maintenance practices to prevent future failures and optimize asset performance. Additionally, conducting a thorough cost-benefit analysis specific to your industry and assets can provide valuable insights into the most cost-effective approach for your organization.
Proactively maintaining your assets
With the technological strides we are making today, there exists many tools to support your company’s ideal maintenance strategy. TRACTIAN’s sensor, Smart Trac, collects real-time data on your asset’s asset vibration and temperature, and makes it available to maintenance teams on their phone, tablet, or computer, 24/7.
With the collected information, the system generates prescriptive insights about various failure modes and operation status; supported by artificial intelligence and machine learning, the conditioning-monitoring system alerts you before assets or components totally, or even partially, fail. This data enables you to create a predictive maintenance strategy, optimize maintenance tasks, and streamline work orders – keeping your production on track, and downtime at a minimum.