
Implementing Takt Time to Improve Your Process
By The Maintainers • January 04, 2024
Takt time, sometimes referred to as Takt, is a key principle of lean manufacturing. It refers to the rate at which you need to complete a product or service to satisfy customer demand.
The Takt time formula in Lean can be represented as below:
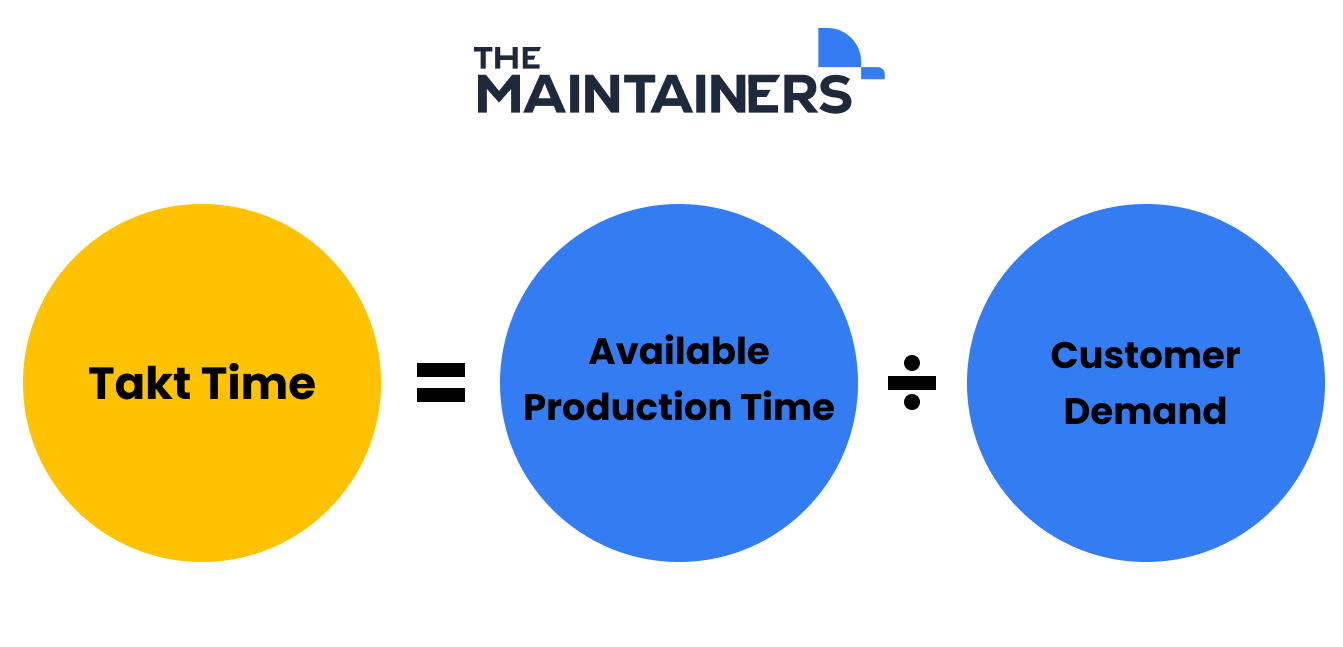
Available Production Time refers to the total amount of time available for production during a specific period, and Customer Demand means the amount of products or services that customers require during the same period. This is expressed as a rate or quantity, such as units per day, hours per week, or calls per hour.
For instance, if a customer needs an order fulfilled every two hours, you, as the producer, must ensure you can finish making that product in two hours or less. if a toothbrush factory operates 480 minutes per day and customers demand 240 toothbrushes per day, Takt time is two minutes. Similarly, if customers want two toothbrushes per month, Takt time is two weeks. This sense of consistent timing is why Takt time is often referred to as the heartbeat of a lean production system.
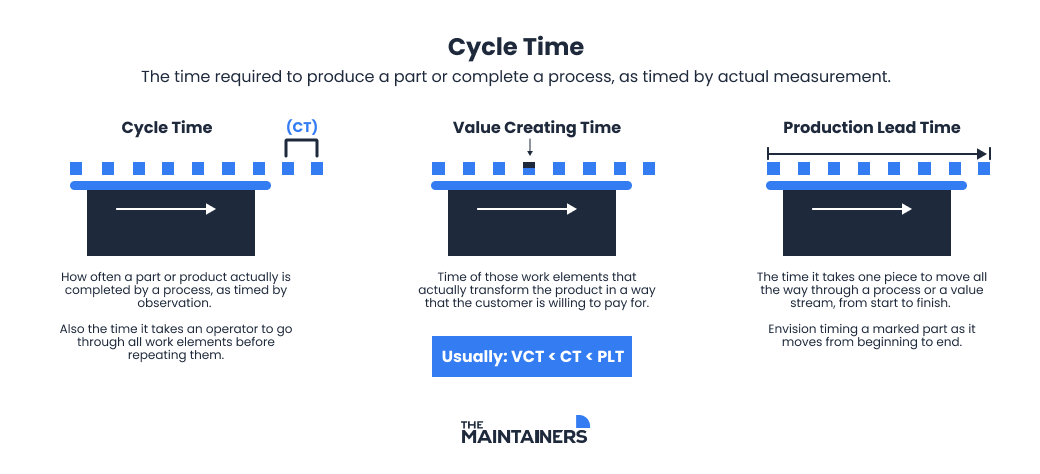
Why are the Benefits of Takt Time?
Takt optimizes your team’s efficiency and productivity, as well as reduces instances of waste. It helps you maintain a continuous work flow and ensures otimized storage space as you avoid over or under production.
Production Alignment: Takt time synchronizes production rates with customer demand, preventing overproduction or underproduction and ensuring a smooth workflow.
Waste Reduction: By adhering to Takt time, companies can minimize waste, optimize resource utilization, and identify and eliminate inefficiencies in the production process.
Customer Satisfaction: Takt time helps meet customer demand consistently, reducing lead times and enhancing customer satisfaction through timely product delivery.
Continuous Improvement: As a metric, Takt time serves as a baseline for continuous improvement efforts, enabling teams to set performance targets, measure results, and identify opportunities for ongoing enhancements.
Efficient Resource Planning: Takt time facilitates efficient workforce planning by indicating the necessary staffing levels to meet customer demand, helping companies optimize their workforce and avoid unnecessary costs.
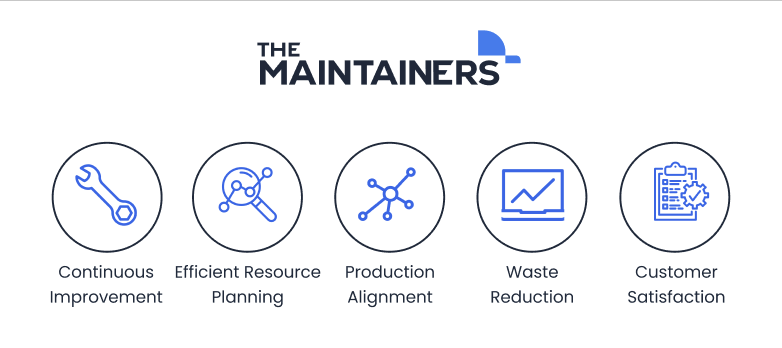
Other benefits of Takt are:
Reducing works in progress (WIP),
Builds a foundation for value stream mapping,
Identification of bottlenecks,
Standardized work routines,
Providing a data-centric basis for scheduling, and;
Providing a real-time target for operators to “win the shift.”
Takt ensures customer satisfaction is met, while reducing efficiencies on the production line.
While takt time is a valuable concept in lean manufacturing, it does have some limitations and considerations:
Demand Variability/Assumption of Stable Demand: Takt time may be less effective in industries with unpredictable or highly variable customer demand.
Complex or Inconsistent Products/Processes: It may not suit industries with complex products or processes requiring flexibility beyond a fixed production pace.
Neglects Quality Considerations: Takt time focuses on production rates and may not explicitly address quality concerns if not balanced with appropriate measures.
Limited Flexibility: The fixed nature of takt time may pose challenges in dynamic environments, where sudden changes or disruptions require a more flexible production approach.
While takt time is a powerful tool for many manufacturing contexts, its effectiveness depends on the specific characteristics of the industry, the nature of the products, and the reliability of demand forecasting. It’s important to recognize its limitations and consider alternative approaches in situations where these limitations may impact its applicability.
How Does Takt Relate to OEE?
Overall equipment effectiveness is a valuable metric that has an end goal of “perfect” production, i.e. an ideal cycle time (100% performance) with no defects (100% quality) and no planned or unplanned downtime (100% availability).
Takt time is more relevant to production efficiency than effectiveness/OEE, where 100% efficiency is characterized by takt; good pieces equals target count/production.
In simple terms, the target for OEE is ideal cycle time, whereas the target for efficiency is takt. Ideal cycle time is the theoretical fastest time for a production process, and includes no budgeted losses. And takt, again, is the cycle time that aligns demand with production.
While OEE is a valuable metric for manufacturers, operators find efficiency to be often more meaningful, as it has a very obvious interpretation. A good efficiency score means your plant is efficient. OEE metrics on the other hand are more vague, as they are relative.
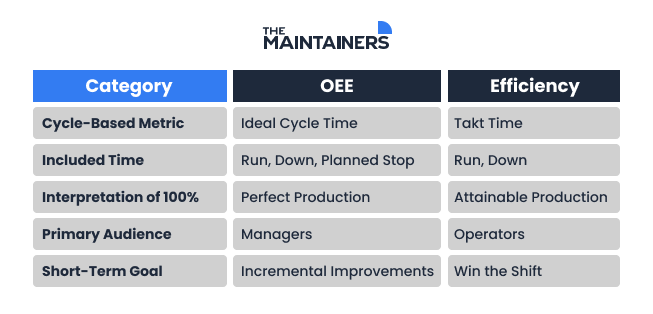
Takt time serves as a powerful tool in enhancing both maintenance and production processes. By establishing a synchronized rhythm that aligns with customer demand, Takt time minimizes waste, optimizes resource utilization, and fosters a more efficient workflow. This strategic approach not only supports production efficiency but also enables proactive and preventive maintenance, ensuring that equipment and processes remain reliable and operational, contributing to overall organizational success.