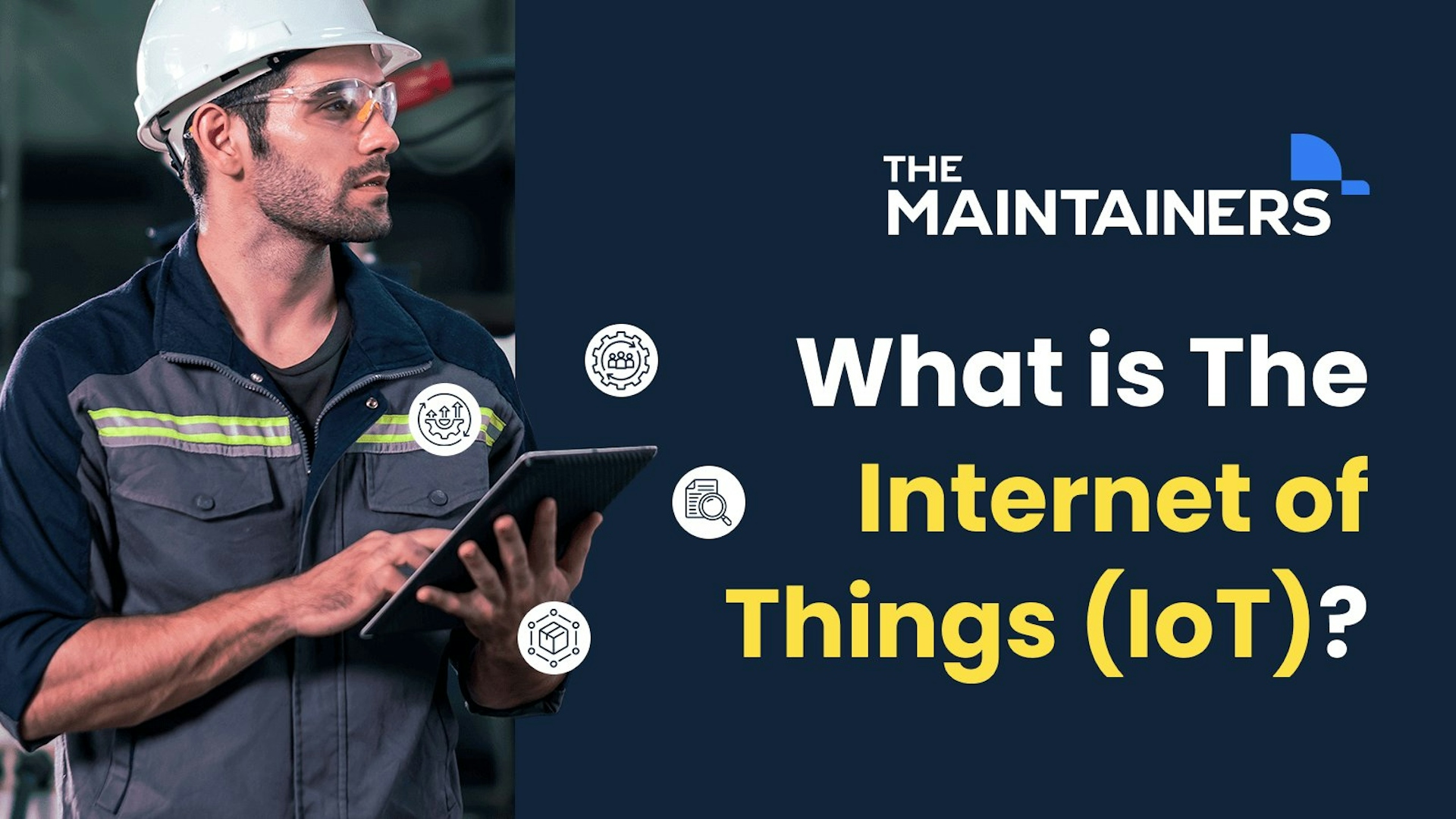
Unlocking Total Reliability: How the Internet of Things is Revolutionizing Industries
By The Maintainers • October 12, 2023
What is the Internet of Things? The Internet of Things (IoT) represents a transformative force in the digital landscape, heralding a new era of interconnectedness and automation. At its core, IoT is a network of physical devices, vehicles, buildings, and even everyday objects, all equipped with sensors, software, and connectivity capabilities. These components work in unison to collect, exchange, and act upon data, creating a seamless web of communication between the physical and digital realms. This technological paradigm shift has far-reaching implications, impacting industries, cities, and our daily lives. From smart homes and smart devices that adapt to our preferences, to industrial processes optimized for efficiency, IoT is reshaping the way we interact with the world around us. In this rapidly evolving landscape, understanding the intricacies and potential of IoT is not only crucial for businesses and industries but also for envisioning the future of a more connected, intelligent world.
What role does IoT play in manufacturing and maintenance?
IoT devices hold immense relevance in the domains of manufacturing, maintenance, and reliability, transforming traditional processes and enabling a new level of efficiency and productivity.
Key benefits of using IoT sensors in maintenance include:
Real-time Monitoring: IoT sensors provide continuous, real-time data about the condition and performance of equipment. This allows for immediate awareness of any anomalies or issues.
Predictive Maintenance: By analyzing data from IoT sensors, maintenance teams can predict when equipment is likely to fail. This enables proactive maintenance, reducing the likelihood of unexpected breakdowns.
Condition-based Monitoring: IoT sensors can track specific parameters like temperature, humidity, vibration, and by constantly collecting data. By monitoring these conditions, maintenance teams can address potential problems before they escalate.
Reduced Downtime: With predictive maintenance, repairs and replacements can be scheduled during planned downtime, minimizing disruptions to operations.
Increased Reliability and Availability: With IoT sensors letting you know when assets need attention before problems occur, your machinery becomes much more reliable and operationally available.
Increased Equipment Lifespan: By addressing issues early and ensuring equipment is operating optimally, IoT sensors can extend the lifespan of assets, reducing the need for costly replacements.
Cost Savings: Proactive maintenance and reduced downtime lead to significant cost savings. Unplanned repairs, emergency replacements, and other maintenance costs can be expensive, and preventive measures can mitigate these occurrences.
Improved Safety: IoT sensors can monitor for potentially dangerous conditions, alerting maintenance teams to take corrective action before an incident occurs.
Data-driven Decision-making: The data collected by IoT sensors can be analyzed to make more informed decisions about maintenance schedules, equipment upgrades, and resource allocation.
Remote Monitoring: IoT sensors can be accessed and monitored remotely, allowing for off-site maintenance teams to track equipment performance and conditions without physically being on site.
Compliance and Reporting: IoT sensors can help ensure that equipment meets regulatory and compliance standards by providing a record of its operating conditions.
Customizable Alerts and Notifications: Maintenance teams can set up alerts to be notified when specific thresholds or conditions are met, allowing for timely intervention vs periodically scheduled maintenance.
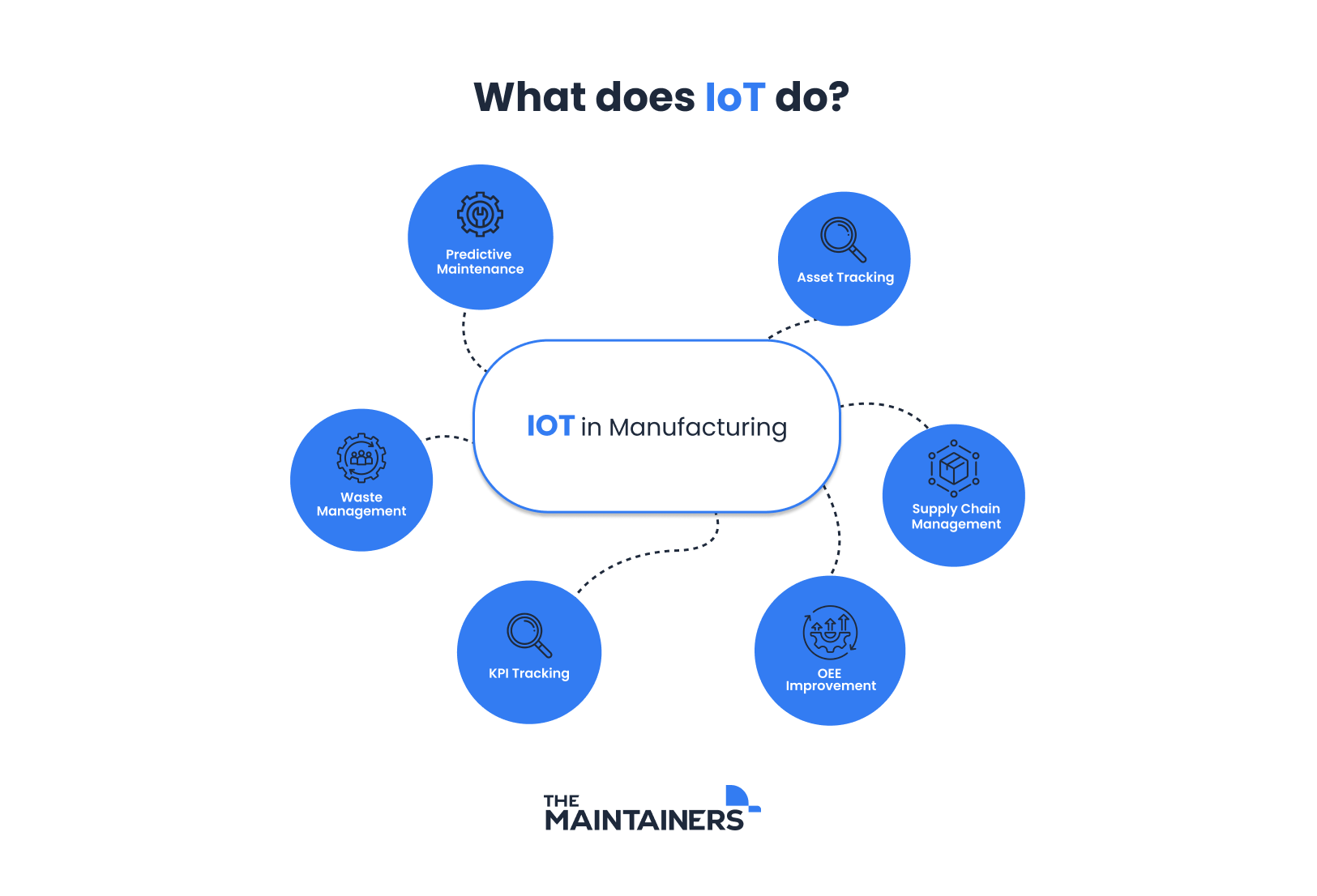
IoTs in Predictive Maintenance
Through IoT-enabled tracking devices, manufacturers can monitor the location, status, and functionality of assets in real-time, and these devices are capable of collecting a vast amount of data. This data can be analyzed to gain insights into production processes. For instance, it can reveal patterns of inefficiencies, allowing for optimizations in the production line and reduced costs.
Historically, maintenance technicians had to manually inspect an asset’s condition — known as condition monitoring — a time-intensive task that often left significant data gaps and provided a limited view of the asset’s behavior and long-term condition. Despite these scheduled inspections, components and assets were still bound to fail without warning. With IoT sensors, data is collected constantly, guaranteeing that instances of abnormal behavior or the development of a pattern does not go unnoticed.
In maintenance, historical data can be used to predict when maintenance should be performed, reducing both unscheduled downtime and over-maintenance. Sensors can be integrated into production processes to monitor quality parameters. If a product falls outside acceptable limits, it can be flagged for further inspection or rectification before it reaches the customer, improving overall product quality. In the context of maintenance, IoT sensors can be used to monitor metrics such as vibration, temperature, hour meter, and energy consumption. By collecting and analyzing this data, it becomes possible to predict when an asset is likely to fail, enabling preventive maintenance tasks to be identified, vs. corrective maintenance occurring when an asset has significantly degraded, or has already failed—overall improving a team’s maintenance strategy.
Beyond saving manufacturers time and money, it also improves a plant’s safety, and the safety of the teams working with dangerous assets. For instance, if a piece of equipment is at risk of exploding due to a sudden increase in pressure, operators can be warned well in advance and rectify or avoid the situation.
TRACTIAN’s online vibration and temperature monitoring sensors provide proactive maintenance for your most critical assets. With the ability to detect over 70 different types of faults, and a patented vibration analysis algorithm that can detect the most subtle behavioral changes in an asset and generate insights about the fault, all your team needs to do is follow the prescribed remedy to prevent damage and potential failure.
With our integrated app’s newly revamped Overview tab, you have a comprehensive view of your assets and their real-time status on a single page. You and your maintenance team can take advantage of the AI-driven predictive system’s ability to warn you of likely issues before they happen, which includes a prioritized list of actions that need to be taken to avoid failure—keeping reliability and availability at peak levels.
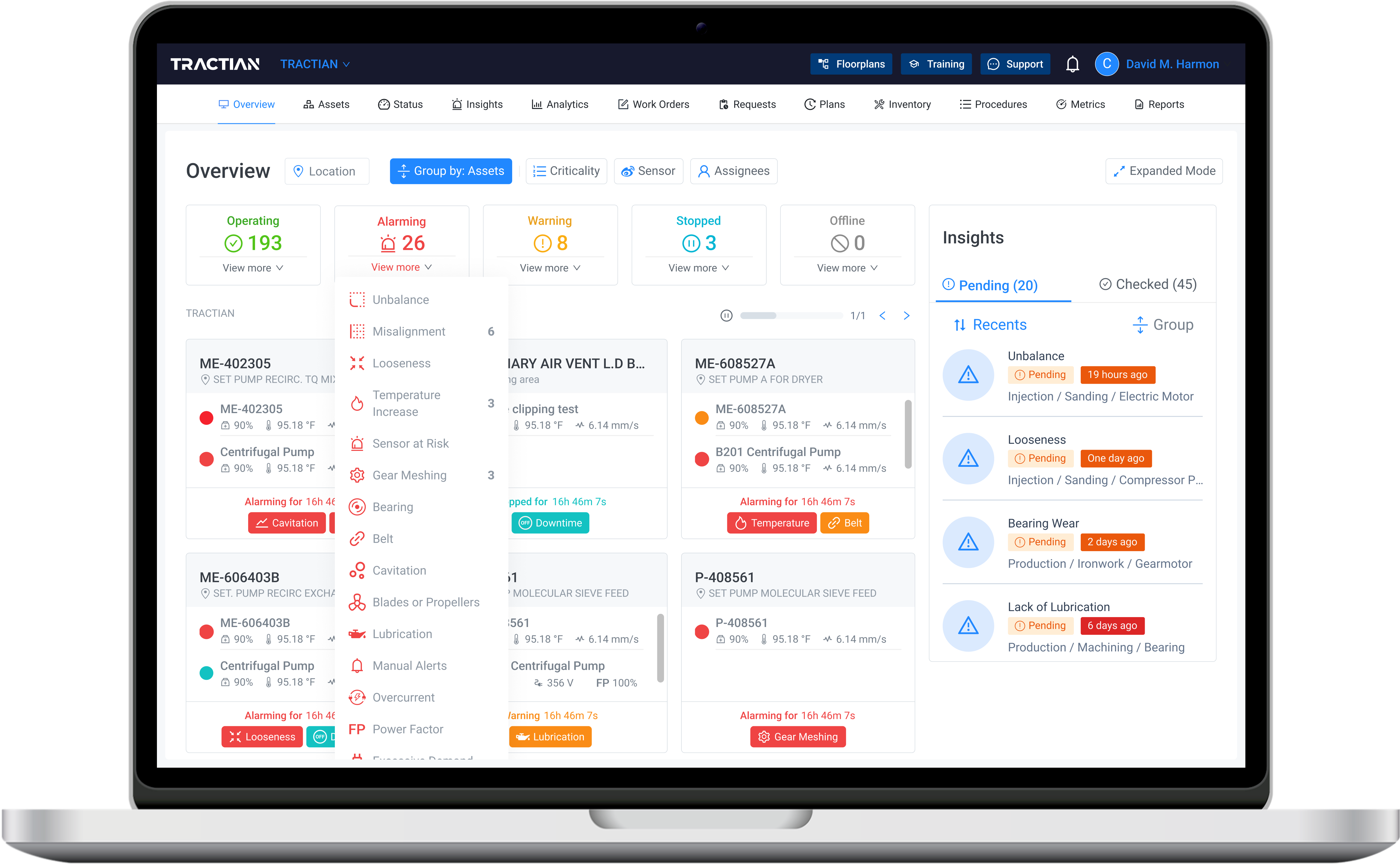
Reduce downtime and improve your assets’ reliability today with TRACTIAN.