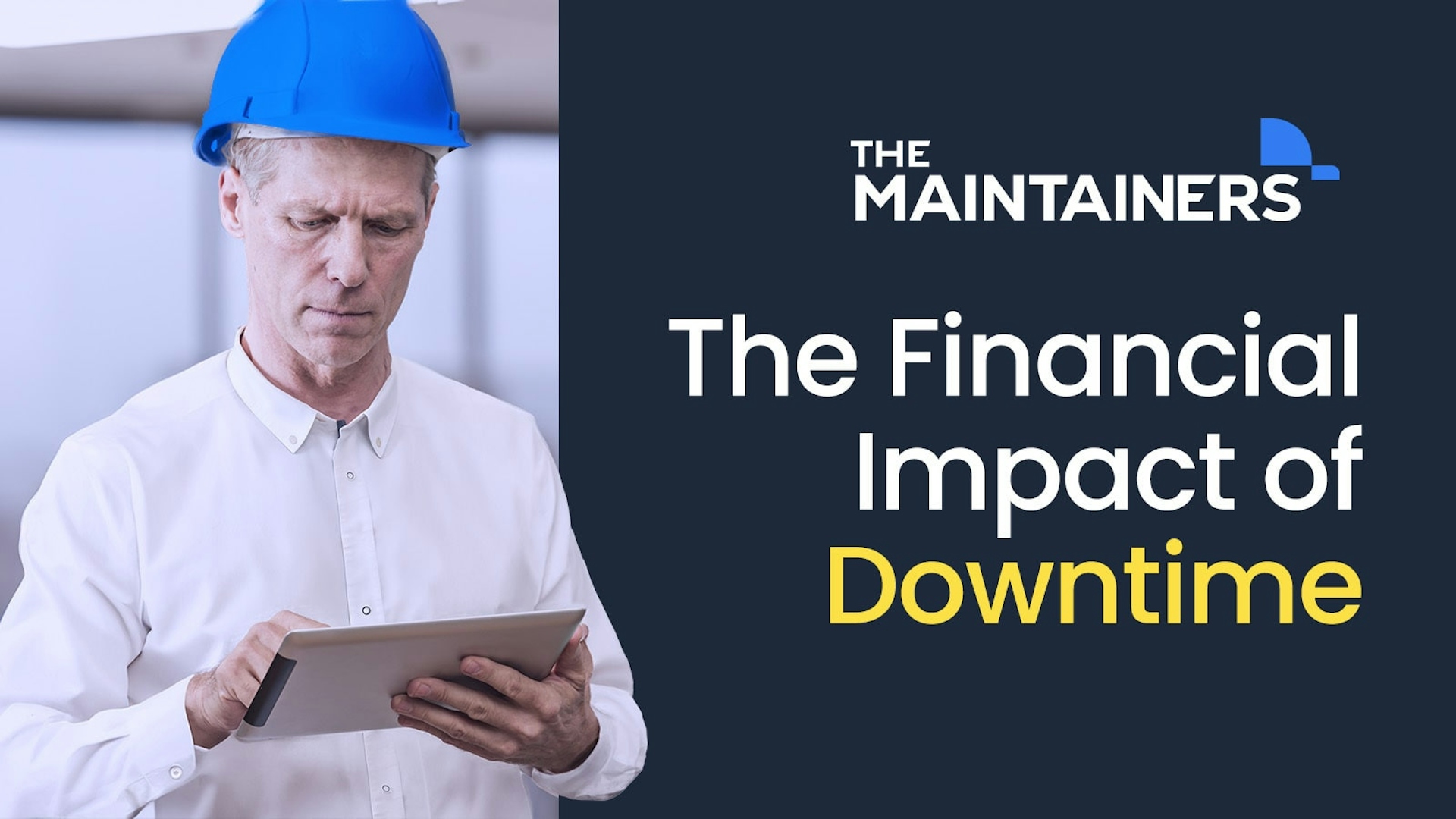
The Cost of Downtime: What’s the Impact on Your Bottom Line
By The Maintainers • October 05, 2023
Time is money, and that saying is especially true in the manufacturing industry. Asset efficiency is the key to successful operations and profit; in turn, production delay of even a few moments can have significant financial repercussions. “Downtime” is the period of time a machine is inactive, inoperable and/or non-functional—operations (and profit) are interrupted, while costs mount.
What is Downtime?
Downtime refers to the period during which a production system or specific equipment is not operational and unable to perform its intended functions. It represents the time when production activities are temporarily halted or delayed due to various factors. Not all downtime is bad: downtime can be caused by scheduled maintenance and product/process changeovers. However when downtime is unplanned, whether it be due to material shortage, component damage, asset failure, or even unforeseen organizational issues, there are significant financial implications, as it leads to lost production capacity and revenue. Additionally, downtime can disrupt supply chains, delay customer deliveries, and negatively impact overall operational efficiency.
The impact of downtime extends beyond the loss of revenue through produced goods, but also includes secondary costs such as wages for staff who can’t work and those involved in rectifying the problem, the cost of emergency spare parts, and potential penalties such as contractual compensation.
A Siemens’ report published earlier this year found that unplanned downtime is currently costing large manufacturing and industrial organizations at least 50% more than it did two years ago. Due to rampant inflation and increased production capacity, Fortune 500 companies lose almost $1.5 trillion a year through unplanned downtime—a 65% rise in two years, and approximately 11% of their turnover.
The Cost of Downtime
While the cost of downtime differs within the industrial sector and by each individual manufacturer, a general equation is represented as follows:
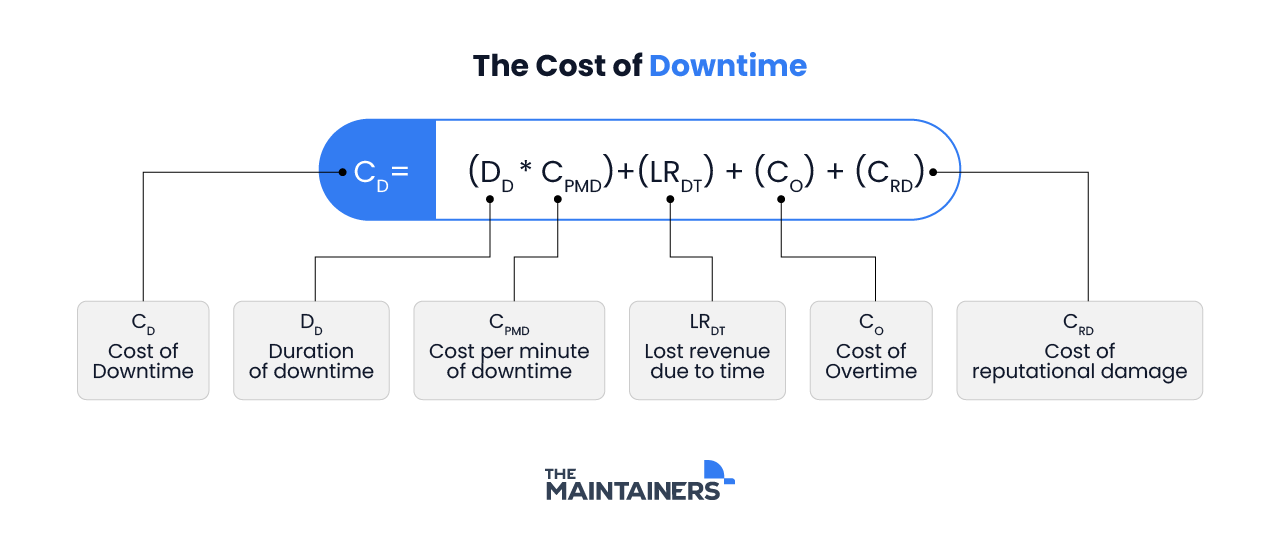
There are other factors that play a role in the actual cost of downtime, both direct (lost revenue, repair costs, etc) and indirect (lost sales opportunities, damage to customer relationships etc.) and other elements relevant to specific operations and industry context. While the above equation is not designed to provide an accurate number, it can guide you with a fair estimate of the financial impact of downtime on your operations.
Siemens’ report highlighted that while production plants are getting better at minimizing the number of unplanned downtime incidents, overall costs of downtime have skyrocketed, costing almost $500,000 per hour of downtime in the oil and gas sector and over $2 million per hour in the automotive sector.
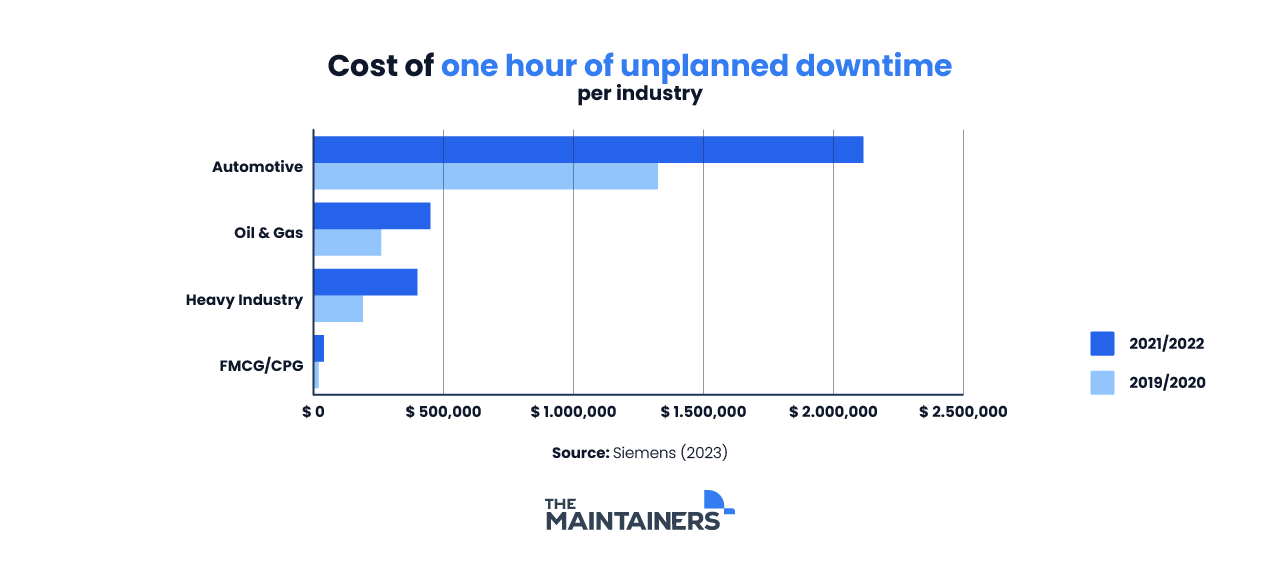
These losses have steadily increased due to rising inflation, stressed supply chains, and the simple fact that operational capacities have improved. Manufactured and processed goods are getting more expensive, with higher sales prices and lack of component availability—such silicone chips and microchips, both facing global shortages—capping production capacity. This means every minute of lost production is especially impactful, and getting assets back up and production lines running is of utmost importance. In the auto industry particularly, downtime in one asset can impact production through a bigger portion of the plant.
Reducing downtime is more than a matter of repairing assets and machinery when they fail. Research has found that in order to effectively combat unplanned downtime and counter losses, facilities should strategically plan maintenance schedules, leveraging real-time data, and take advantage of technological advancements such as record digitization, condition monitoring, and predictive maintenance practices.
Using Predictive Maintenance to Tackle Downtime
The average manufacturing facility suffers 20 downtime incidents a month – six fewer than two years ago. This reduction is largely attributed to the increasing presence of preventive maintenance strategies and teams.
Predictive maintenance leverages the use of real-time data and analytics to predict when equipment and assets are close or likely to fail, allowing for maintenance to be performed when needed. This proactive approach prevents unexpected breakdowns and downtime, as issues are addressed before they escalate. In order to most effectively implement a predictive maintenance strategy, data that is more useful and comprehensive must be collected from assets to correctly analyze its history, patterns, and expected future behavior.
Implementing Internet of Things (IoT) sensors on assets that monitor and track factors such as vibration and temperature guarantee no key data points are missed and that real time insights are always available. Connectivity to an integrated platform like an Enterprise Asset Management (EAM) system allows maintenance teams to efficiently address issues as they’re identified, negating the need for constant physical asset checks and unnecessary maintenance tasks.
TRACTIAN’s predictive system links IoT sensors capable of tracking a variety of asset data with the TracOS™ maintenance management software that then receives, classifies, and analyzes this data. With seamless Artificial Intelligence (AI) and machine learning integration, the platform proactively offers recommendations for asset management and maintenance, guaranteeing minimal operational downtime and maximized asset performance. Not only are potential problems highlighted, but the system also suggests the most appropriate type of maintenance needed to avoid that failure.
Developing and implementing a predictive maintenance plan is the most successful way you can tackle downtime and reduce its impact on your operations’ bottom line. Predictive maintenance stands as the pinnacle of efficiency and reliability in maintenance strategies. By harnessing data-driven insights, it anticipates issues before they escalate, allowing for precise, timely interventions. This approach minimizes unplanned downtime, maximizes asset availability, and ultimately, ensures uninterrupted operations—a game-changer in modern industry.
Reference:
The True Cost of Downtime 2022. Siemens. 2023