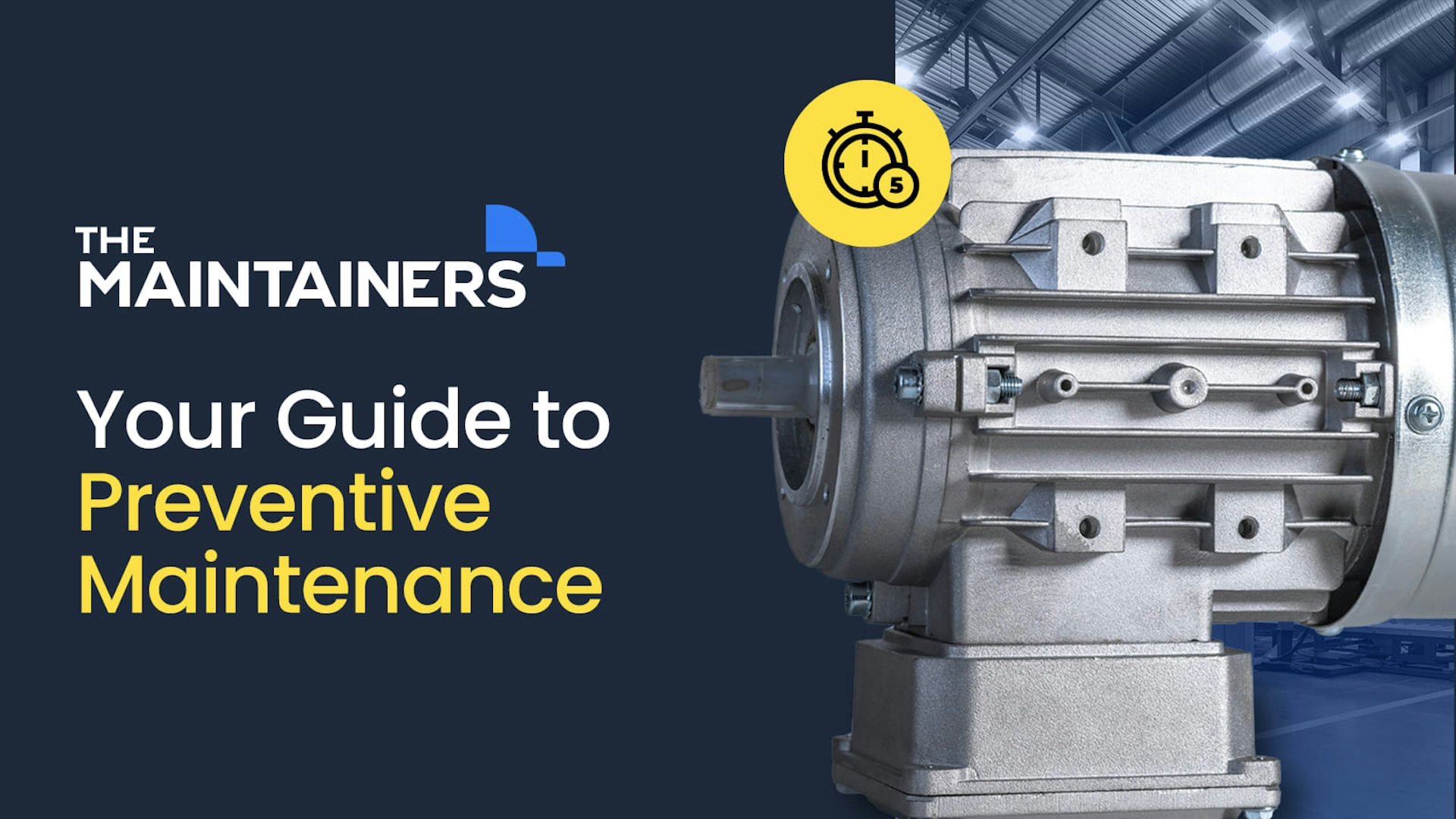
The Ultimate Preventive Maintenance Guide
By Igor Marinelli • May 12, 2023
As a maintenance worker, don’t keep avoiding failures when you could prevent even running into them. Also known as preventative maintenance, preventive maintenance is a strategy used by maintenance and reliability teams in industrial plants.
This strategy detects, replaces, and repairs components and assets before failures can occur. This, in turn, reduces equipment failures and downtime, as well as increases plant reliability and efficiency.
What Is Preventive Maintenance?
Preventive maintenance (PM) is a type of planned maintenance with a goal of fixing problems before they arise. It’s the most simple and cost effective strategy available.
The main goal of preventive maintenance is to avoid unexpected downtime, increase equipment reliability, and extend its lifespan. By performing routine checks and maintenance tasks established by predetermined inspection routes, potential problems can be identified and resolved before they escalate into major issues.
Preventive maintenance programs work to decrease the chance of equipment failure, which usually arises from the improper operation of machines. These activities include periodic reviews, routine lubrication, calibrations, and inspections, among others.
Types of Preventive Maintenance
There are three main types of preventive maintenance: time-based, condition-based, and usage-based.
These three types of preventive maintenance aren’t mutually exclusive, and can be combined in a comprehensive maintenance strategy. Choosing the right maintenance type depends on factors like how critical equipment is, manufacturer recommendations, operating requirements, and available resources.
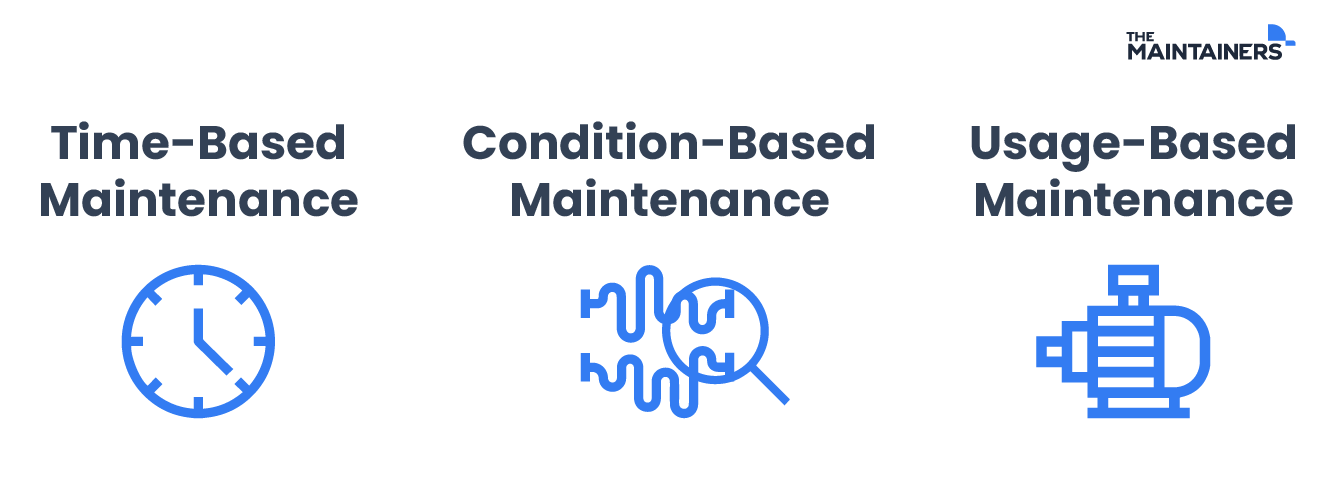
Time-Based Maintenance
Time-based maintenance, or TBM, is measured by the usage time of the physical asset in question. Since it’s based on a schedule, maintenance managers might decide to do something like monthly visual inspections of certain equipment.
TBM activities are scheduled, periodic, and fixed in the maintenance plan. They don’t generally require specialized labor, meaning they can be executed by the maintenance team’s own operators.
It can be a great technique for seasonal maintenance. However, be careful of replacing equipment before necessary or missing a fault because of the time between inspections.
TBM helps maintenance and reliability teams save resources, extend equipment lifespan, improve operating efficiency, and prevent accidents. Many teams set shorter intervals for these preventive tasks, which can lead to unnecessary stoppages and replacements. You can avoid this by combining TBM with a more assertive, data-based technique.
Condition-Based Maintenance
Condition-based maintenance, also known as condition monitoring or CbM, is performed after the time-based maintenance plan. It’s based on the actual condition of the component or asset.
A main tool of condition monitoring is predictive maintenance. Using techniques like vibration analysis, thermography, oil analysis, and acoustic emission, CbM monitors asset condition. With real-time data collection and detailed diagnostics, these tools allow you to define, plan, and implement a preventive maintenance system.
Unlike time-based, condition-based maintenance requires advanced technical knowledge; it’s usually outsourced to specialist companies. That being said, technologies have emerged in recent years that can fill this need. They’re easy to implement and control, requiring no specific training.
Usage-Based Maintenance
Usage-based maintenance (UBM) has maintainers monitor and service equipment based on its actual usage. Instead of performing maintenance tasks at fixed intervals, UBM factors in the number of operating hours, cycles, or distance traveled.
Usage-based maintenance mainly works to optimize maintenance activities by aligning them with the actual wear experienced by equipment. Monitoring usage data in real-time allows maintenance to be performed when specific thresholds are met.
Implementing usage-based maintenance often involves artificial intelligence (AI) and IoT technologies like sensors, data collection systems, and predictive analytics. By analyzing the data, maintenance teams can make informed decisions about when and how to perform maintenance tasks.
Benefits of Preventive Maintenance
Compared to corrective or reactive maintenance, preventive maintenance services offer several benefits. Here are some advantages of implementing this type of strategy:
- Increased Equipment Reliability: By maintaining equipment, you can minimize unexpected downtime and ensure that the equipment always operates reliably.
- Cost Savings: By addressing minor problems early on, you can prevent them from developing into more significant and costly issues. Additionally, routine maintenance helps extend the lifespan of equipment, postponing the need for expensive replacements.
- Enhanced Safety: Preventive maintenance helps identify and correct safety hazards, ensuring that assets operate safely and in compliance with regulations.
- Improved Efficiency and Performance: Cleaning, lubricating, and calibrating components can improve efficiency, reduce energy consumption, and enhance overall performance. This, in turn, can lead to increased productivity and cost savings in the long run.
- Minimized Downtime: By implementing preventive maintenance, you can minimize unexpected downtime and maintain a smooth workflow.
- Improved Planning: Better planning of labor, spare parts, and equipment optimizes their efficiency and reduces the likelihood of emergency situations.
- Regulatory Compliance: In certain industries, regulatory bodies may require regular maintenance and inspections to ensure compliance with safety and environment standards. Implementing preventive maintenance helps meet these requirements and avoids potential penalties or legal issues.
- Extended Equipment Lifespan: Keeping components in good condition allows us to prevent excessive wear and tear. By addressing issues promptly, you can maximize the usable life of your assets, delaying the need for costly replacements.
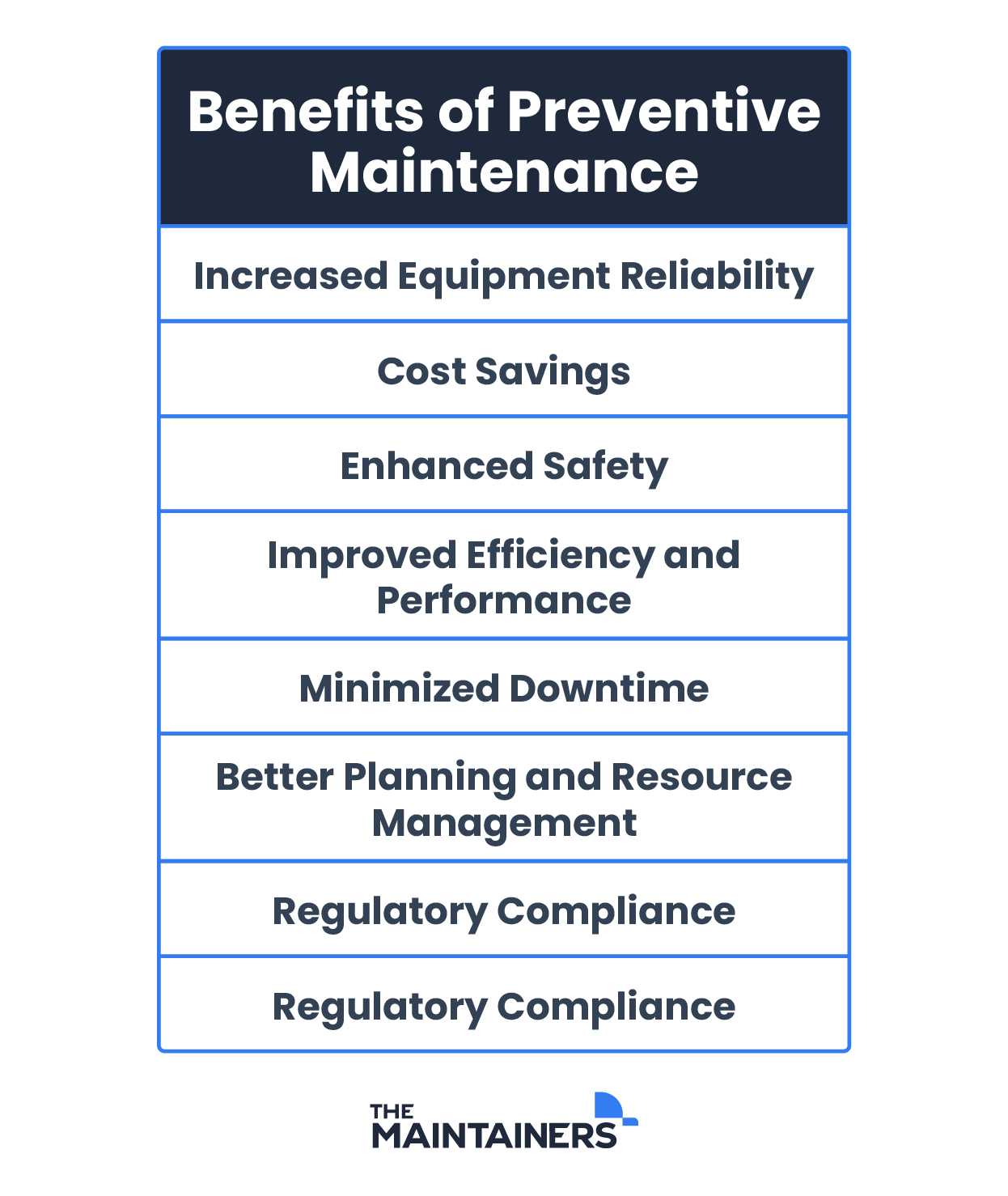
Overall, preventive maintenance is a proactive and strategic approach to equipment maintenance. This results in increased reliability, reduced cost, improved safety, and enhanced efficiency.
Examples of Preventive Maintenance
Here are some examples of preventive maintenance tasks commonly performed across various industries:
- Inspections: Regular visual inspections of equipment and machinery to check for signs of wear, damage, leaks, or other anomalies.
- Lubrication: Applying lubricants to moving parts to reduce friction, prevent corrosion, and ensure smooth operation.
- Filter Replacement: Replacing filters in HVAC systems, air compressors, or machinery to maintain proper airflow, prevent clogging, and optimize performance.
- Calibration: Occasionally calibrating instruments, sensors, or gauges to ensure accurate measurements and reliable readings.
- Cleaning and Clearing: Removing dust, debris, and contaminants from equipment, vents, and filters to prevent overheating, blockages, and reduced efficiency.
- Belt and Chain Replacement: Adjust tension or replace worn belts and chains in machinery.
- Electrical System Maintenance: Inspect, test, and service electrical connections, circuit breakers, and wiring to prevent electrical hazards, malfunctions, or power interruptions.
- Software Updates: Keep software systems, applications, or firmware up to date to ensure security and functionality with the latest technologies.
- Battery Replacement: Test and replace batteries in equipment, emergency lighting systems, or backup power supplies.
- Preventive Repairs: Address issues like loose bolts, worn seals, or damaged components before they lead to more significant failures or breakdowns.
- Fluid Analysis: Regularly analyze fluids, like oil, coolant, or hydraulic fluids, to detect contaminants, degradation, or abnormal levels.
- Parameter Checks: Monitor and adjust operating parameters, like temperature, pressure, or speed, within specified ranges to ensure optimal performance.
The specific preventive maintenance tasks will vary depending on the type of equipment, the industry, and manufacturer recommendations. Creating a preventive maintenance plan tailored to your specific needs is essential for reaping the benefits of proactive equipment maintenance.
When to Use Preventive Maintenance
Because preventive maintenance varies depending on equipment and operation, knowing the best time to use it can be a challenge. Following are a few situations when it’s best to implement this maintenance strategy:
- Consider implementing preventive maintenance based on the age of the equipment.
- Stick to warranty requirements by following the manufacturer’s recommended maintenance schedule.
- Identify critical equipment or systems that, if they were to fail, could cause significant safety hazards, lost production, or financial losses.
- Analyze historical maintenance records, equipment performance data, and failure patterns to identify recurring issues or areas prone to failures.
- Some equipment may require specific maintenance tasks based on seasonal or weather conditions.
- Implement preventive maintenance for newly installed equipment to ensure it operates optimally from the start.
Many companies utilize a preventive maintenance software, or CMMS software, that aids them in creating a plan that suits them.
Developing a customized preventive maintenance plan based on these considerations will help maximize the benefits and effectiveness of the program.
Preventive maintenance is a vital strategy that offers numerous benefits for companies and maintenance workers alike. By addressing issues before they escalate, preventive maintenance enhances equipment reliability, reduces unplanned downtime, and extends the lifespan of valuable assets.
Embracing preventive maintenance isn’t just an investment in equipment. It’s a commitment to operational excellence, sustainability, and long-term success.