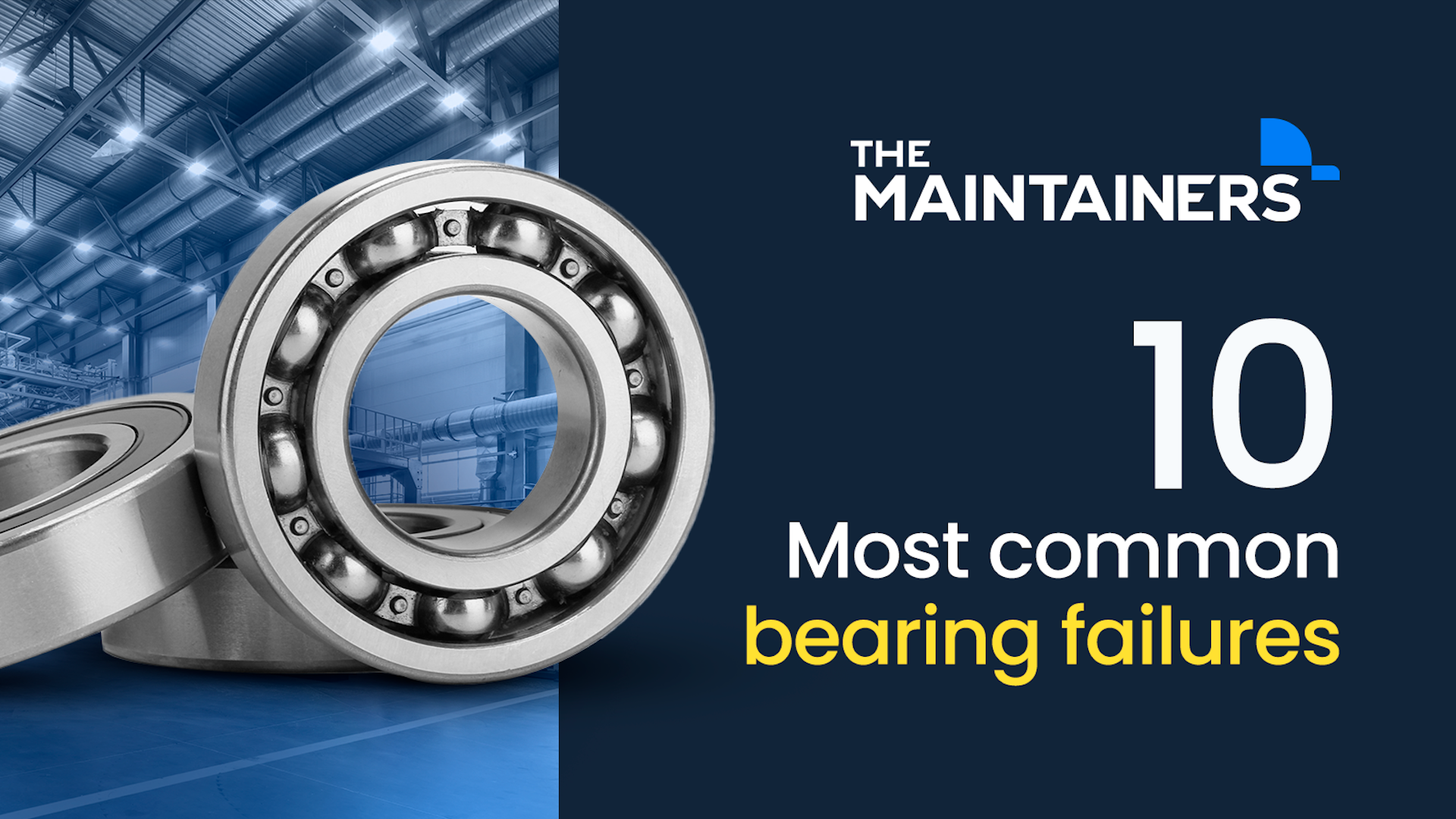
10 Reasons Your Bearings Fail
By Igor Marinelli • May 17, 2023
Bearings support rotating machinery, making them a vital part of all production processes, and crucial to the operation of machines including motors, pumps, and conveyors. They enable the smooth rotation of shafts and other moving parts, thereby reducing friction and wear. Large manufacturers work hard to make sure these components meet the highest quality standards, so they can also ensure the highest reliability levels.
Some bearings will fail prematurely, affecting assets and entire production lines, besides leading to costly downtime and production losses. Luckily, there are steps you can take to understand these problems. If maintainers can intervene when issues are still at an early stage, they can address them before they cause too much damage.
The following are the most common causes of bearing failure, different bearing failure modes and, most importantly, ways to prevent them. Understanding these is essential for improving bearing performance and reliability.
Except for those that have been pointed out, the images in this article are by maintenance management and bearing reliability expert Alejandro Pérez Martínez. Find the original post here.
1. Lubrication
About three quarters of premature bearing failures are the result of poor lubrication. This is because one of the most vital parts of a well functioning bearing is the lubricating film created through the viscosity of the base oil.
Bearings require a sufficient amount of lubricant to reduce friction and prevent metal-to-metal contact between the rolling elements and raceways. Inadequate lubrication can lead to excessive heat buildup, which can cause the lubricant to break down and the bearing to fail.
Some of the causes of these issues include: inadequate lubricants, excessive quantities of lubricant, lubricant degradation, or shortage.
Failure Mode
The most appropriate way to detect lubrication failures is through ISO 15243, which classifies different modes that occur in rolling bearings made of standard bearing steels. It can be recognized by abrasive wear, adhesive wear, and fatigue of the raceways; lapping, scratches and discoloration are common.
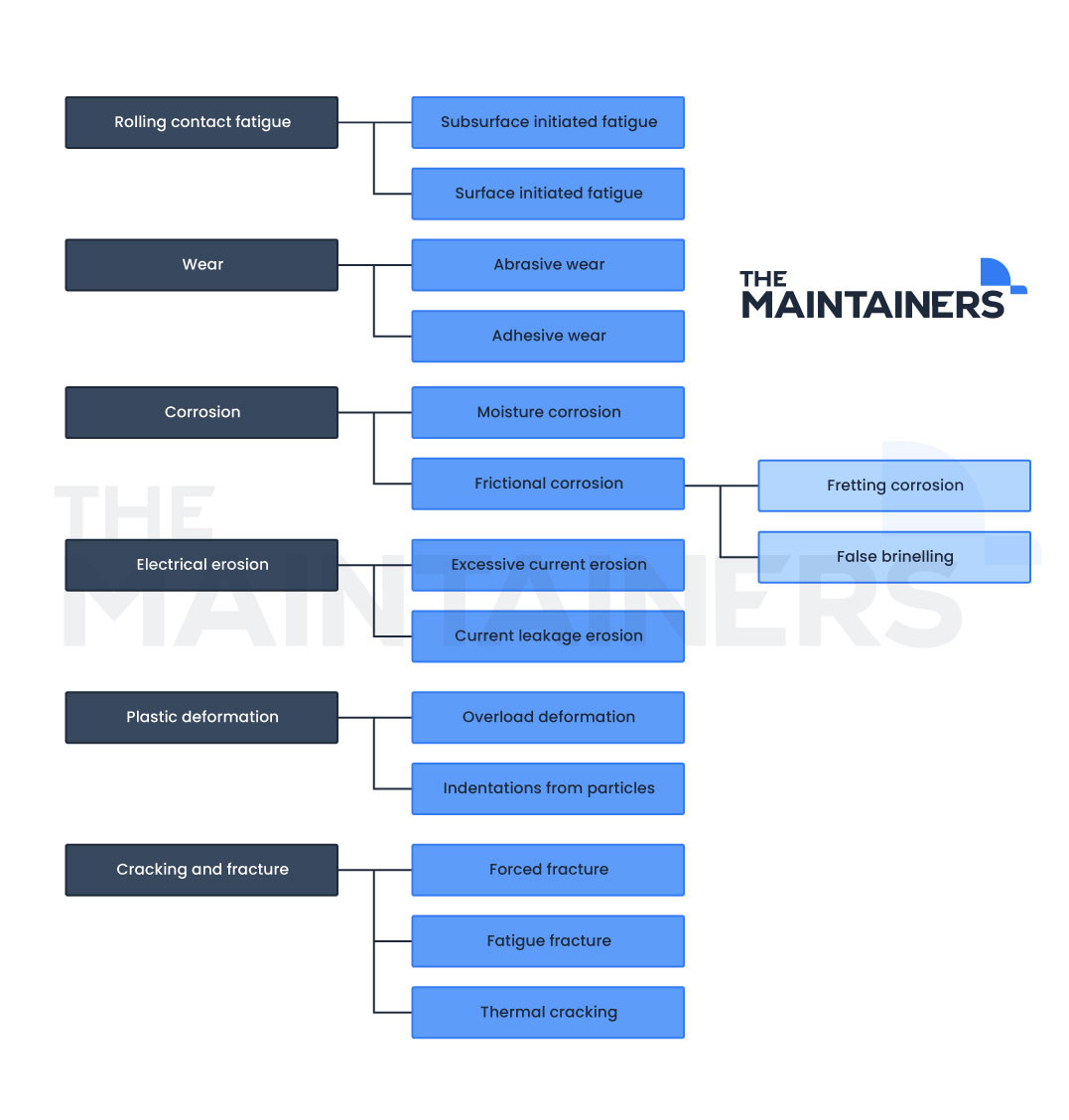
How to Prevent Damage
Lubricant type, amount, application frequency, placing, method, and condition all play a role. They should all be precisely aligned in order to prevent and reduce bearing damage.
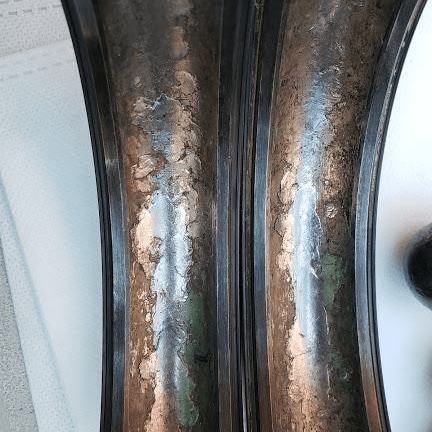
2. Contamination
Contamination is caused by foreign substances – such as dust, dirt, and water – typically contained in the lubricant at the time of application, or by the process itself where the operating bearing is. This causes damage to the rolling elements and raceways.
Contamination can also lead to corrosion, which can further degrade the bearing’s performance. Common sources of contamination include dirty work environments, improper handling, and improper storage.
Failure Mode
Dents on the raceways, on the rolling elements, formation of micro craters, and fan-shaped tracks.
How to Prevent Damage
Ways to prevent contamination induced damage include: implementing procedures focused on lubricant storage, filtering new lubricants, identifying and labeling to avoid miscibility, keeping work areas clean, and doing grease fittings. Remember to use clean gloves to reduce the risk of contamination, and improve sealing systems.
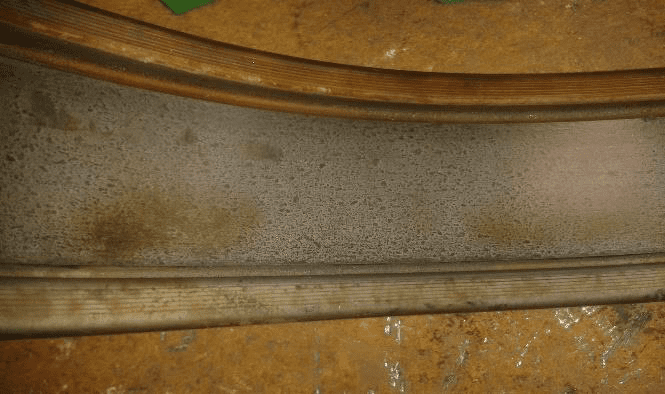
3. False Brinelling
False brinelling is caused by vibration between rolling elements and raceways, improper transportation or storage. It can also occur in backup or emergency equipment due to vibration transmissibility.
Failure Mode
Some failure modes include discolorations in reddish tones at the same distance from the rolling elements, impressions of the rolling elements on the raceways, and shearing on the tracks.
How to Prevent Damage
First, implement transportation procedures for repaired equipment by securing the shaft. Then, properly store bearings isolated from vibration, dust, and high ambient temperature. Continue on to carry out maintenance tasks for the operation of backup equipment.
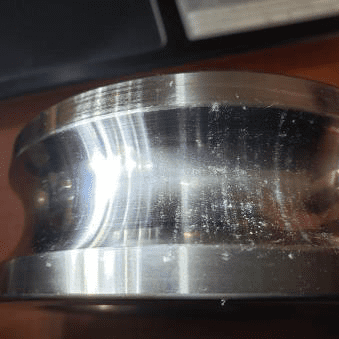
4. Fretting Corrosion
Fretting bearing corrosion can also be called loss of interference fit at the shaft or housing level. It’s caused by improper machining of the contact surfaces, shaft, or housing – typically the rotating ring, which is the one with the tightest fit. It can also be caused by fixing one of the bearings but not allowing axial expansion.
Failure Mode
When surfaces are not in full contact with each other a chemical reaction takes place, leading to oxidation of the surfaces together with micro movements of the adjacent components. This causes loss of material, and in extreme cases, it can fracture one of the rings.
How to Prevent Damage
Prevent fretting corrosion damage by performing a procedure for each bearing replacement to measure the shaft and housing. With a micrometer, compare it with the machining tolerances: if it is out of dimension and/or shape, proceed to machine it properly. Avoid using glue, “pecking” the shaft, or grinding it.
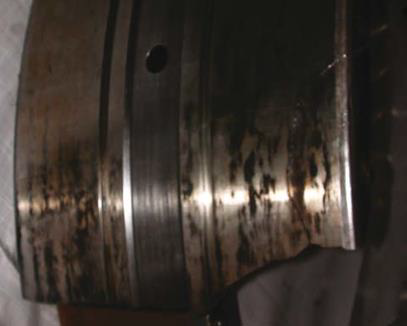
5. Overload
Bearing overload occurs when the bearing is cold mounted through unsuitable methods, like: chisels, punches, direct blows, bronzes, etc.
Bearings must be installed correctly to ensure proper alignment, fit, and clearance. If installed incorrectly, the bearing can experience uneven loading, excessive vibration, and premature wear. Common installation-related problems include incorrect fit, insufficient preload, and incorrect mounting.
Failure Mode
The rolling element – being made of a harder steel than the rings – receives the axial impacts, causing an overload and burying them in the raceways. In initial stages, it can lead to scratches or small craters. In advanced stages, there is a loss of looseness in the cage cavities, causing abrasive wear.
How to Prevent Damage
To avoid overload damage, apply force on the hoop to rotate it over 360°. If that isn’t possible, rotate it at least 180°, follow the recommended mounting instructions, and train your personnel.
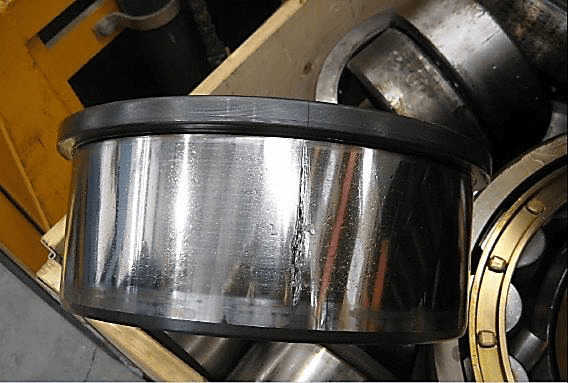
6. Overheating
Overheating is caused by heating the bearing to temperatures higher than 257 °F, which affects dimensional stability. It’s also caused by heating the bearing with blowtorches or oil baths without temperature control.
Failure Mode
When heated above dimensional stability, the bearing undergoes elastic deformation at the molecular level, causing an increase in the amount of oxygen. Its structure crystallizes and loses hardness, thus “clean” fractures can occur with a combination of load and speed.
How to Prevent Damage
In order to prevent overheating you should mount the bearing with an induction heater at a temperature of 230 °F, and train your personnel in the correct use of tools.
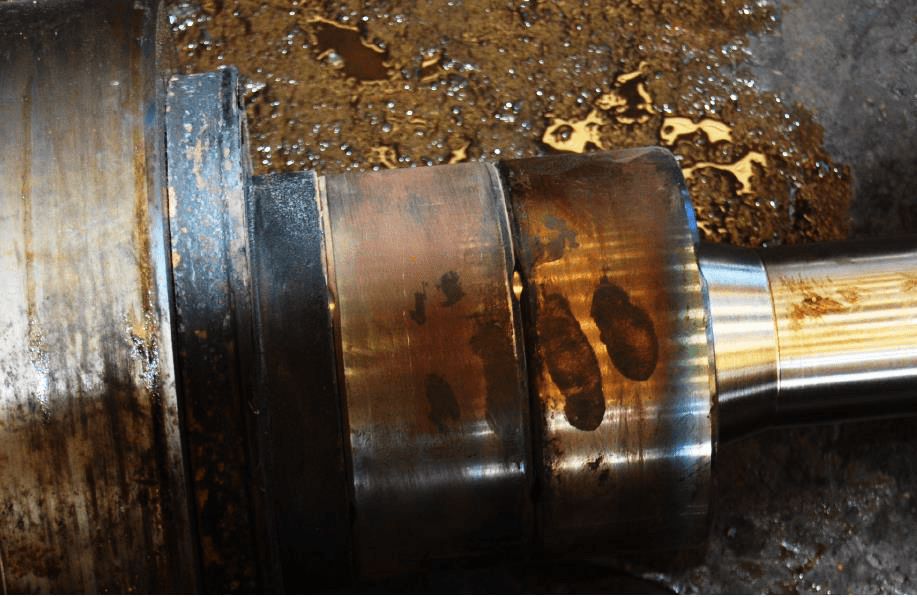
7. Electrical Erosion
Electrical erosion is caused by current flow to the bearing or excessive voltage. It’s mainly a consequence of operating equipment with frequency variators, loss of insulation in connections, electric arc when welding, and grounding on equipment supports.
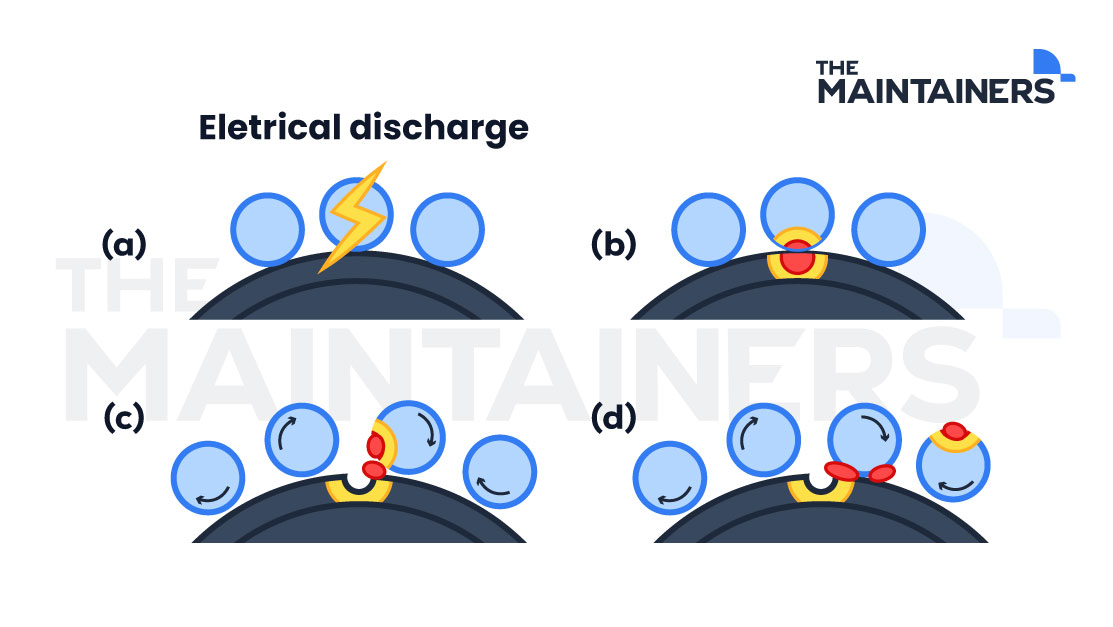
Failure Mode
In the case of excessive voltage, sparks are produced. They pass through the rolling elements causing loss of material, melting the raceways and leading to localized pitting in both the rolling element and the raceway.
In the case of current flow, there is a low current circulating between the bearing components. This causes dents and the development of grooves in the raceway, as well as dark and gray discolorations in the rolling elements.
How to Prevent Damage
When preventing electrical erosion, use insulated bearings to cut off the passage of current. Properly insulate your equipment, and develop procedures for welding work where physical ground locations are indicated.
8. Corrosion Due to Humidity
Corrosion because of humidity is caused by long storage time of equipment with lubricated bearings, or by sealing failures and water ingress in backup – mainly pumping – equipment.
Failure Mode
Condensation or water causes a chemical reaction that leads to oxidation, leaving traces of etching. In the same way, in stored equipment, the oil releases its soap, causing damage.
How to Prevent Damage
Implement a maintenance task for stored equipment where the shaft is frequently rotated, use a lubricant with suitable properties, and improve sealing systems.
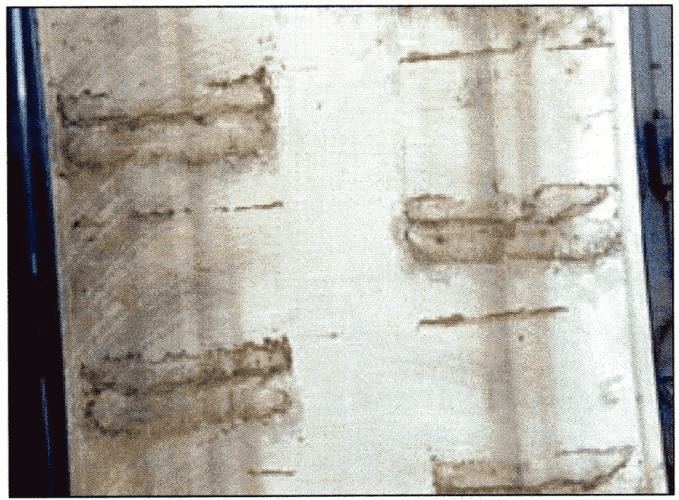
9. Misalignment
Bearing misalignment occurs when not maintaining collinearity between equipment. The stress caused generates overload in the bearing, leading to a decrease in its service life and premature failure.
It can be caused in the same way by an out of shape machining of seats and housings, or by mechanically fixing both bearings and not allowing axial expansion by thermal growth.
Failure Mode
When the bearing is overloaded, there’s premature wear in raceways in the ring, and those rotate around its full circumference. Wear will appear on one side and the static ring will also show wear in the load zone starting on one side, going towards the center and ending up on the opposite side.
How to Prevent Damage
But how to prevent bearing failures, or misalignment specifically? Improve your machining processes, implement proper assembly procedures, train your personnel and align your shafts and pulleys.
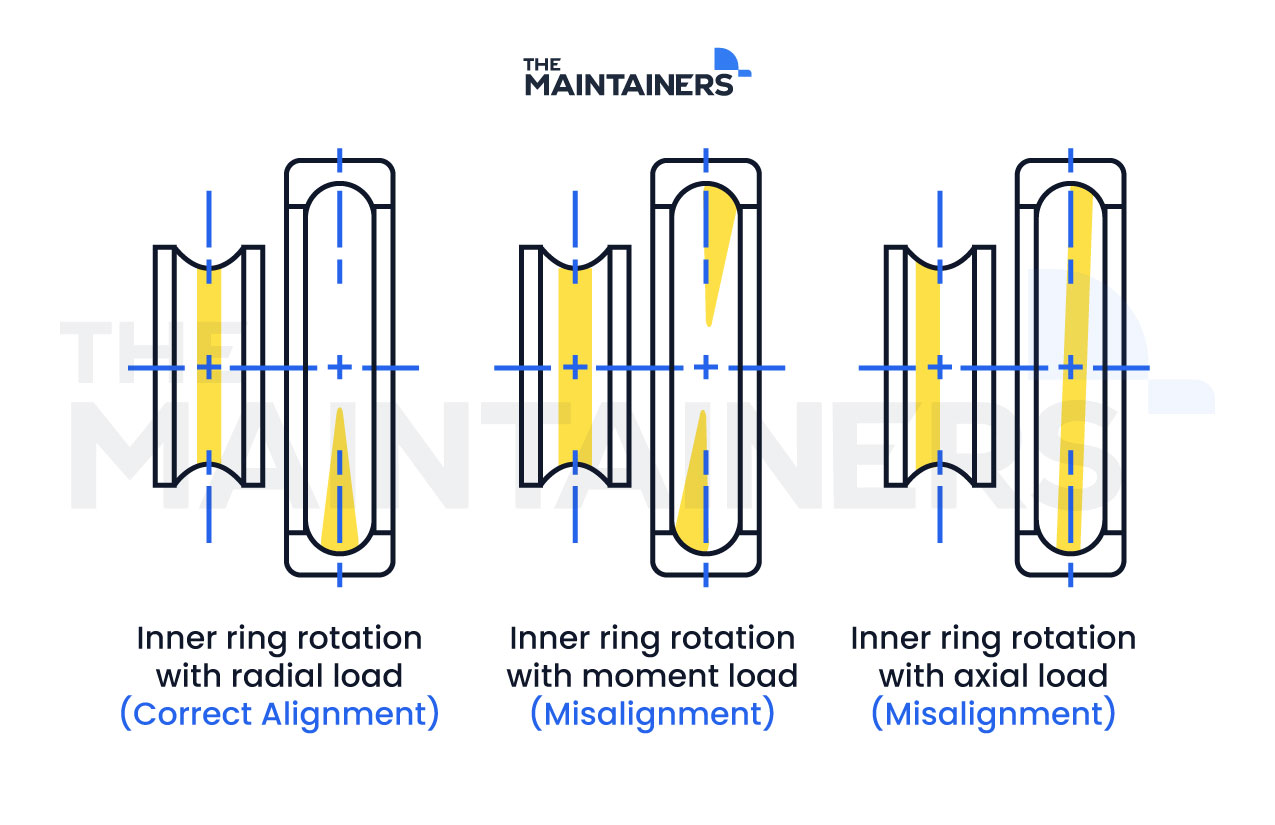
10. Storage and Handling
This occurs when the bearing is not stored correctly. If it’s kept in its original packaging, the damage is caused by external vibrations, long periods of storage with high humidity, and temperature conditions. If it’s out of its packaging, it’s caused by contaminant ingress.
Improper storage can cause premature damage to the bearing even if it’s in its original packaging. There’s a great area of opportunity to improve its storage system, eliminate obsolete bearings, and standardize nomenclatures.
Failure Mode
The bearing receives external vibrations from adjacent machinery or heavy trucks. By storing several bearings horizontally, the rolling elements cause damage. In the case of contaminant ingress, it’s caused by abrasive wear.
How to Prevent Damage
Preventing any damage from storage and handling is simple. You must train warehouse personnel, keep the shelves free of vibrations and dust, control the temperature and humidity of the warehouse, and don’t remove the bearing from its packaging until the moment of assembly. If the packaging is lost, cover the bearing with wax paper and spray it with some type of anticorrosive.
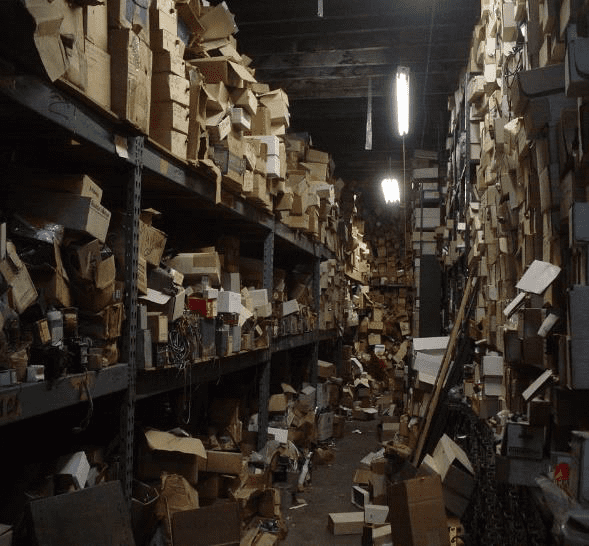
To prevent these failures, it is essential to follow proper maintenance and installation practices, including using the correct lubricant, keeping bearings clean and dry, installing them correctly, and monitoring them for signs of wear and damage.
Establishing procedures, tasks, and standards to take care of bearing condition is vital in an industry setting. Maintaining and keeping up with information about component health will ensure you avoid premature failures by fixing them when they’re in an early stage, thus increasing their life cycles.
By addressing these issues, companies can improve the reliability and longevity of their machines and equipment, reducing downtime and production losses.