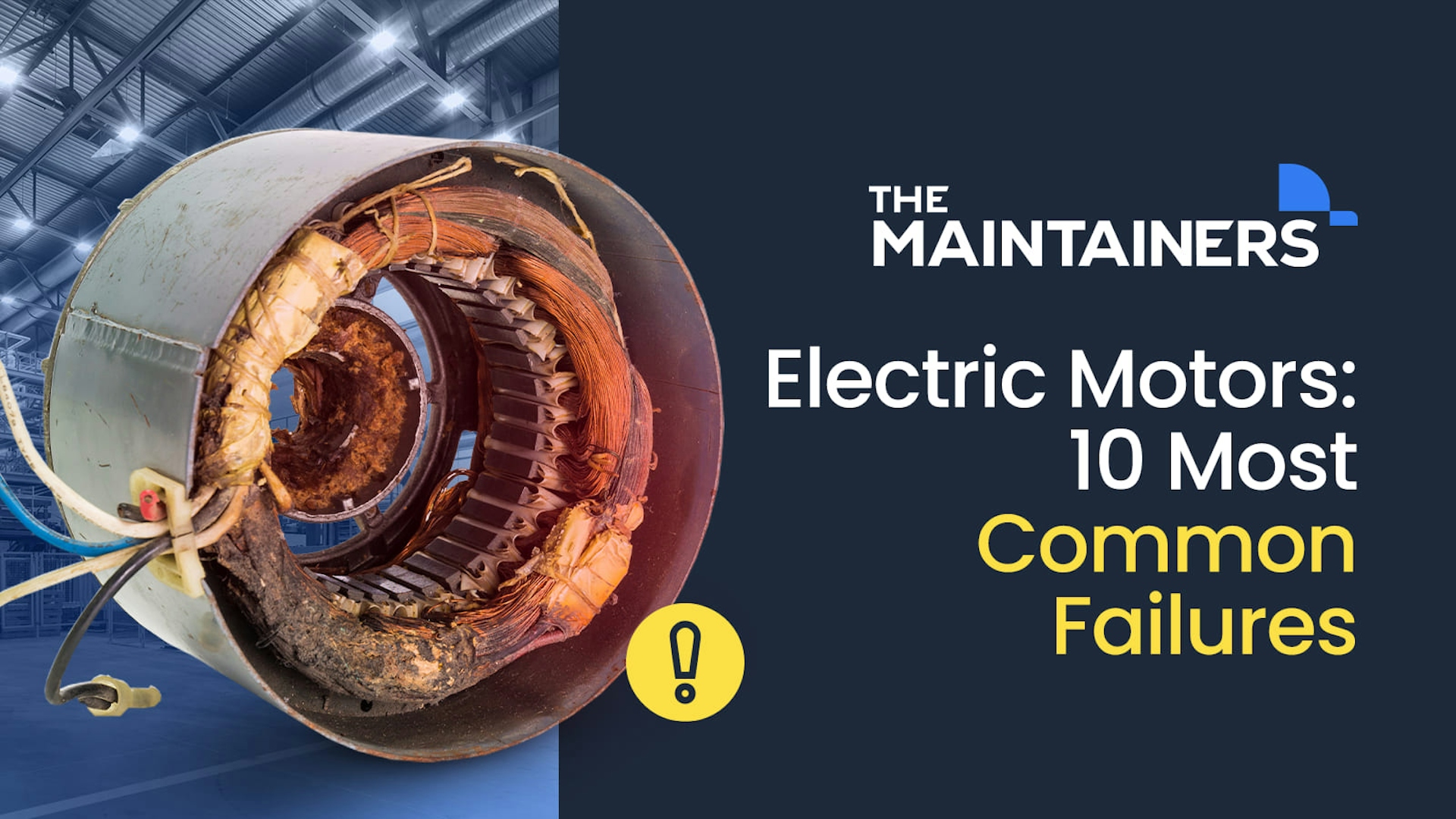
10 Most Common Failures in Electric Motors
By The Maintainers • May 15, 2023
Electric motors are responsible for setting most machines in motion, driving production lines, propelling conveyor belts, and giving mobility to robotic joints, among other purposes. They’re complex and technical assets, and to keep them functioning at peak performance is equivalent to ensuring entire operations run smoothly.
The real challenge of industries worldwide is keeping production lines running without unexpected failures and unplanned downtime.
Remember, both mechanical and electrical issues can lead to motor failure. Having the right knowledge on the root cause of each fault can mean the difference between costly downtime and improved asset uptime.
The issues that lead to failure of electric motors and their components can be of various natures. However, most of them can be avoided with well-trained personnel and the adoption of effective maintenance programs, such as condition monitoring systems capable of predicting possible problems.
1. Misalignment
Misalignment happens when the motor drive shaft isn’t properly aligned with the load, or if the component that couples the motor to the load is misaligned.
This results in mechanical stress, increase in motor wear, and in apparent mechanical load. Another consequence of misalignment is increased vibration in the load and motor.
It can be classified into three types: parallel, angular, or combined. Parallel or radial misalignment occurs, as the name implies, when the center lines are parallel but not concentric.
Angular or axial misalignment is observed from an angle formed between the center lines of the shaft, which cross each other. The shaft center lines intersect but aren’t parallel.
The last and most common type of the three, combined misalignment brings both parallel and angular deviations in the center line.
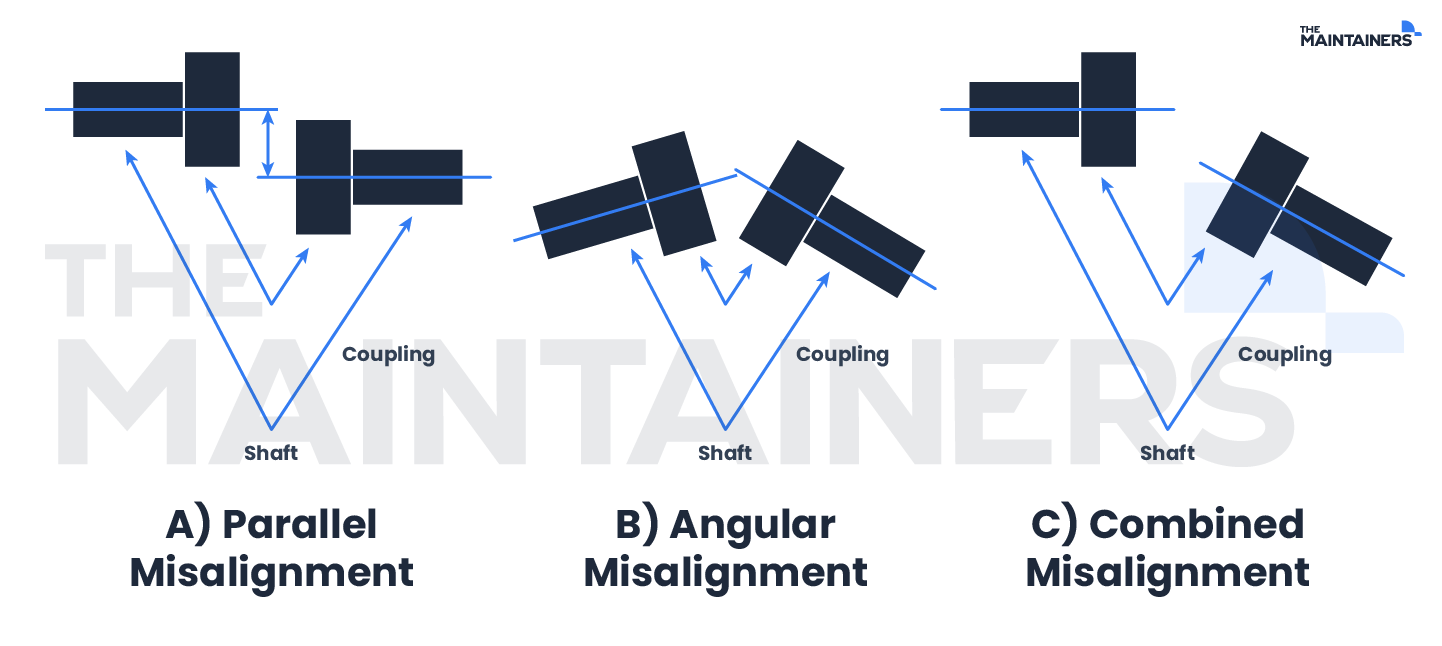
In addition to wear on drive components, misalignment can also lead to issues like premature failures, decreased production capacity, shorter asset life, reduced machine efficiency, and increased machine energy usage.
2. Operational Overload
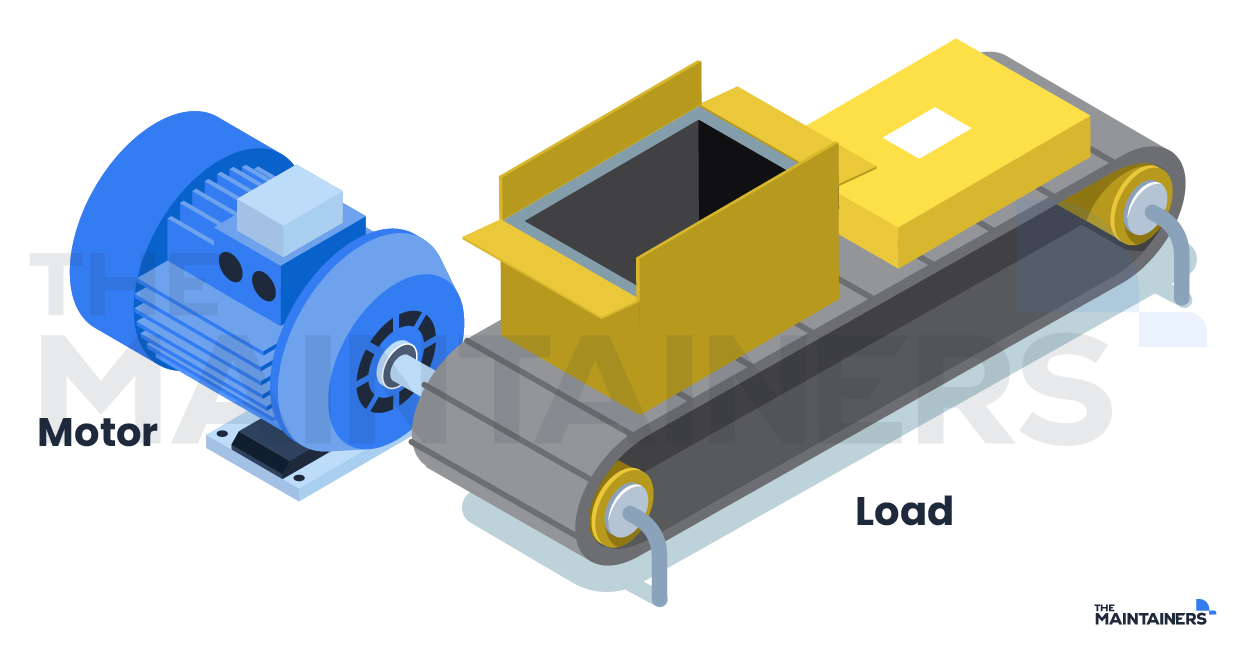
Overload happens when a motor is demanded beyond its rated torque, i.e. the electrical operating current is higher than normal, which causes overheating.
An overloaded motor shows signs including excessive current consumption, overheating and insufficient torque. These are also some of the main causes of premature failure and engine wear.
Because of this, asset life is decreased and the motor’s protection device can be triggered, which will cause a stop in operation and unplanned downtime.
3. Soft Foot
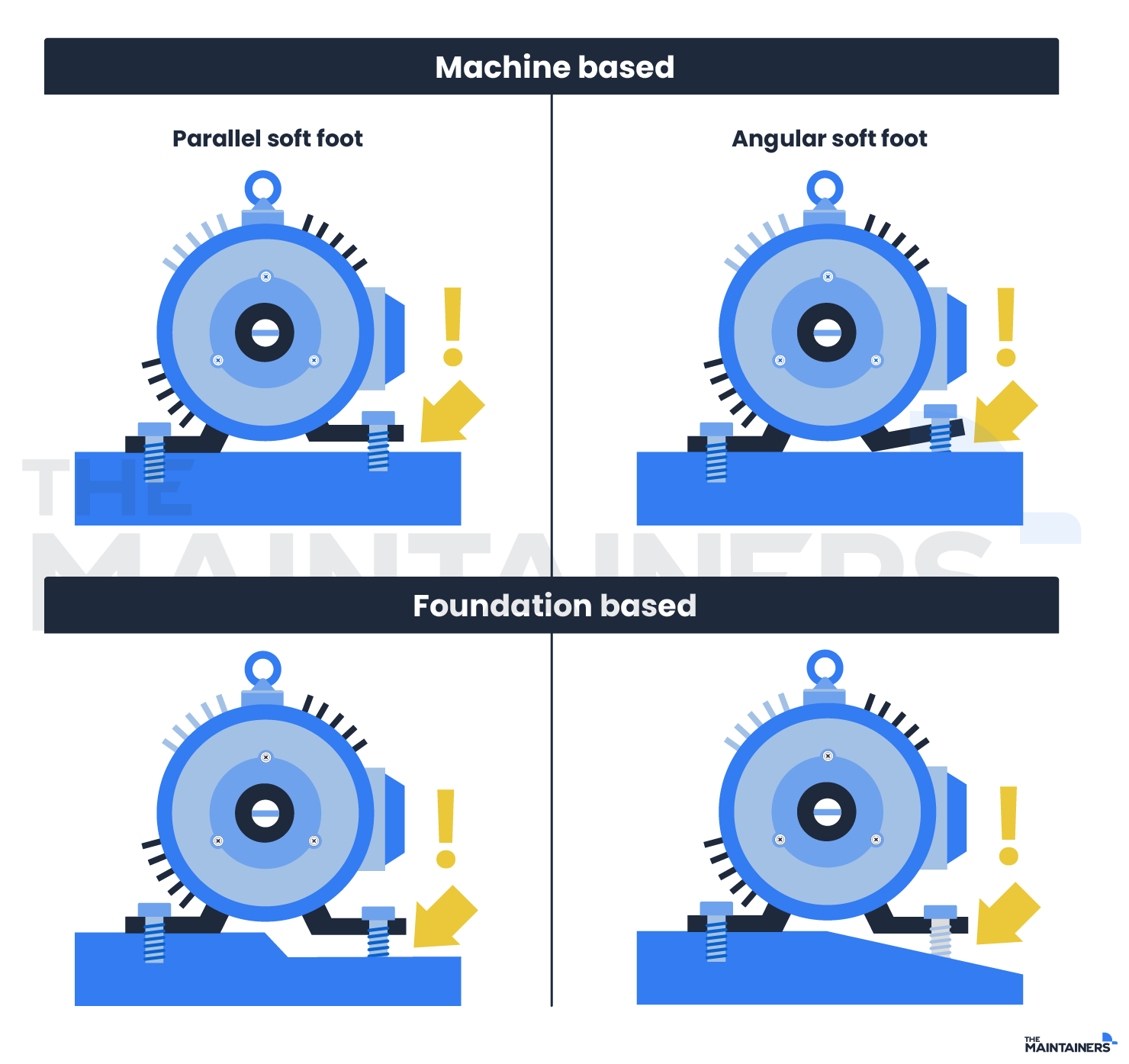
Soft foot conditions happen when the mounting feet of a motor or driving component are not even or seated on the same surface, or the surface itself isn’t even. This can trigger misalignment and mechanical stresses in both the motor and load shafts.
If the feet of a motor are not balanced, an action like tightening the mounting bolts can create new misalignment mechanical stresses. One way to detect the problem is by looking at the attachment bolts and machine base: soft foot is often manifested between two diagonally positioned mounting bolts.
There are two types of soft foot. Parallel soft foot occurs when one of the mounting feet sits higher than the others. Angular soft foot is when one of the mounting feet or base plates isn’t parallel to the mounting surface.
To prevent this, it’s important that the motor and load are mounted in such a way that the seating does not cause any additional vibrations in the asset, nor any transfer of stresses to the motor.
4. Bearing Wear
Bearing failures can occur for several reasons, including heavier than designed load, inadequate lubrication, ineffective bearing seal, induced shaft voltages, misalignment, contamination, among others.
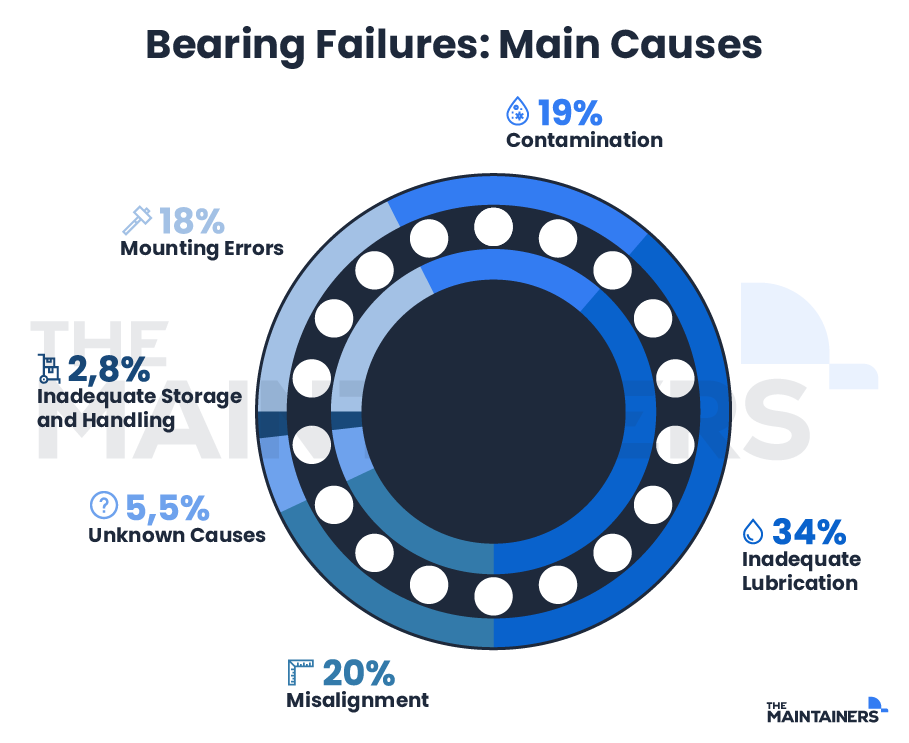
Broadly speaking, we can classify bearing failures into pre-operational and operational. All pre-operational concerns damage that may occur before or during bearing installation, such as: static misalignment, inaccurate shaft and bearing housing adjustment, defective bearing seats on shafts and bearing housings, handling, storage, excessive stress due to the passage of electric current in the bearing and transport, etc.
Operational failures, on the other hand, basically comprise inefficient lubrication or sealing, false brinelling, material fatigue, low resistance, current leakage (due to the passage of electric current through the bearing), and operational misalignment.
Bearing failures often create a cascading effect, accelerating electric motor failures.
If you’d like to learn more about the most common reasons for bearing failure, check out this blog.
5. Shaft Unbalance
This type of unbalance occurs when a rotating part of the center of a mass does not lie on the axis of rotation. This uneven mass distribution generates centrifugal forces that are transmitted to the bearings and can damage the parts of an electric motor, resulting in shortened asset life.
Unbalance can be caused by dirt accumulation, lack of balance weights, uneven mass in motor windings, and manufacturing variations, among other factors.
This type of fault can be classified into static, conjugate, or dynamic. In static unbalance, the main shaft and the shaft around which the machine rotates are parallel, but not coincident.
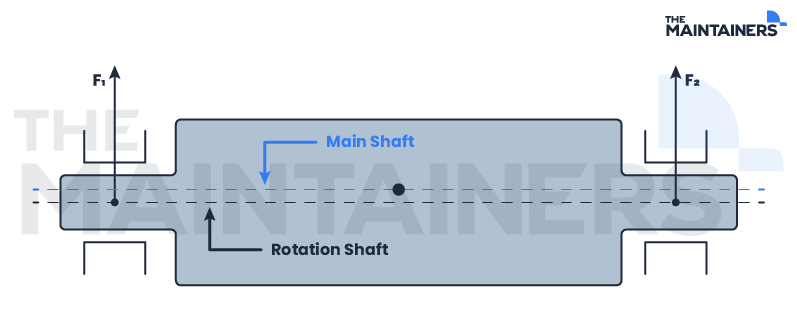
In conjugate unbalance, the axes are not parallel, but there is an intersection between them at the center of gravity of the rotor.
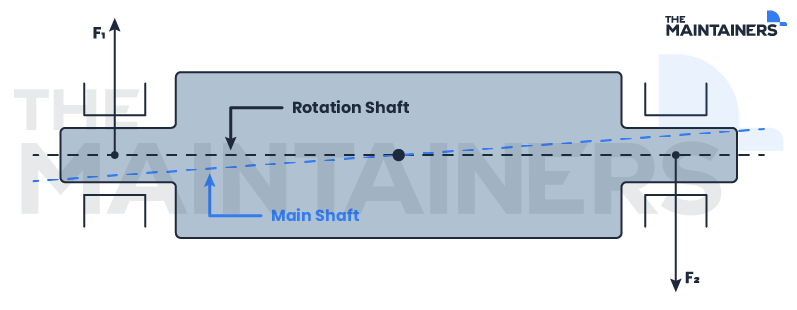
Finally, dynamic unbalance is a combination of static and conjugate, where the main shaft and the rotation shaft are neither parallel nor intersecting.
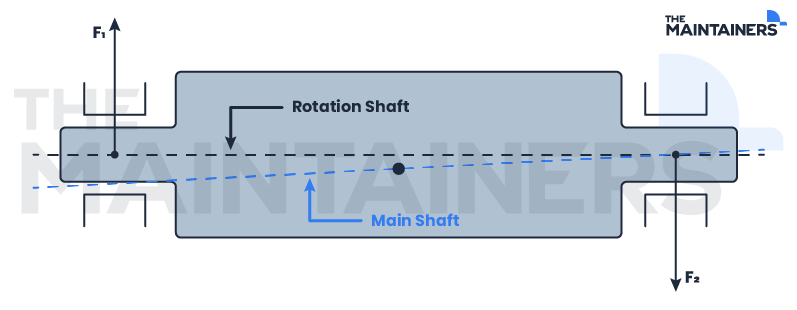
The main consequence here is premature wear on mechanical transmission components, resulting in asset failure.
6. Shaft Looseness
When there’s excessive wear between asset parts, looseness happens – e.g. between the foot and base, or fixed and rotating elements. Mechanical looseness can be divided into Type A, Type B, and Type C.
Type A, or structural looseness, is caused by weakness in the footing, base, or foundation of the asset. It’s usually caused by distortion of the frame or base, deterioration of grouting or ground support, or looseness of bolts supporting the base. It manifests itself in the spectrum as a one-pulse wave per rotation:
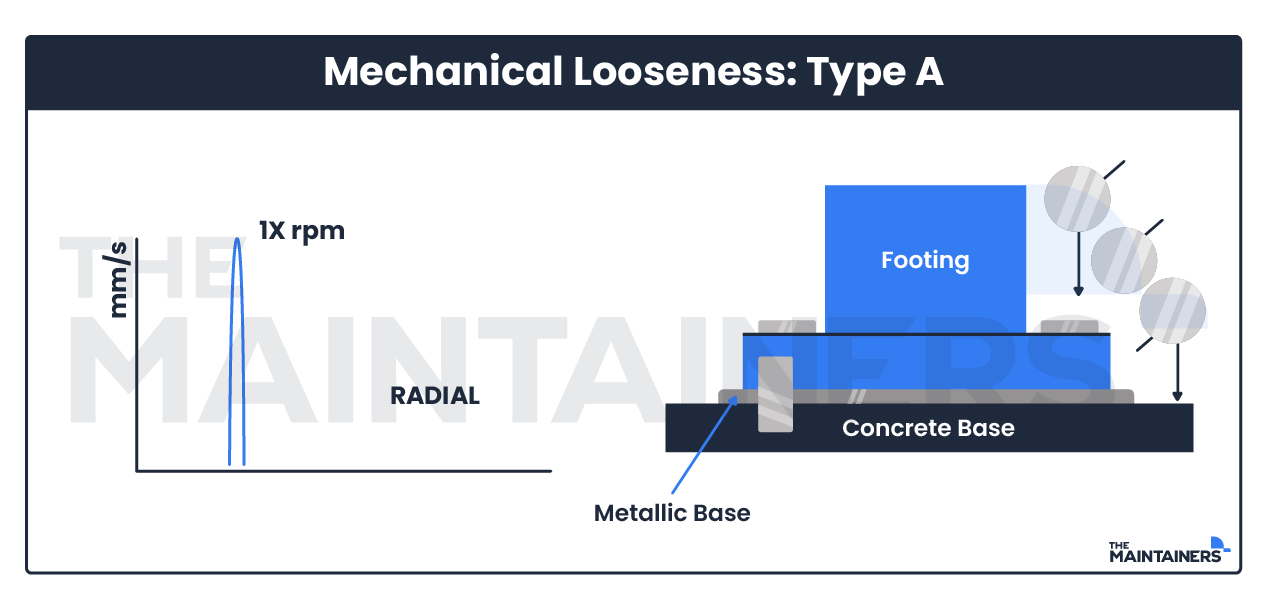
Type B looseness presents itself as loose bolts in the base support, cracks in the bearing pedestal, and/or in the skid frame. In the spectrum, it appears as a time wave of two pulses per rotation:
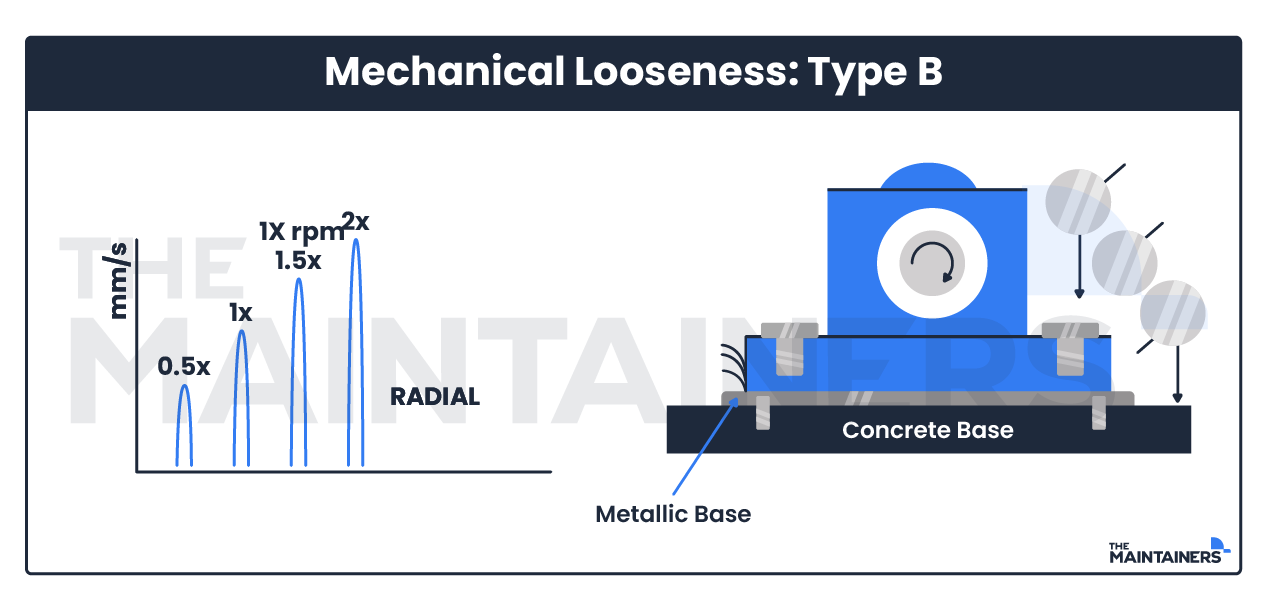
Type C looseness occurs due to an incorrect fit between the parts that make up the dynamic forces of the rotor. It can cause excessive looseness between bearing and sleeve, a loose rotor on a particular shaft, or a loose bushing on the cover, for example.
The appearance in the spectrum features a high noise floor, detecting the looseness – and several harmonics – representing the nonlinear responses of the loose parts. Unlike the A- and B-waves, the time-wave rotations of the C-type loosenesses exhibit a non-repetitive pattern.
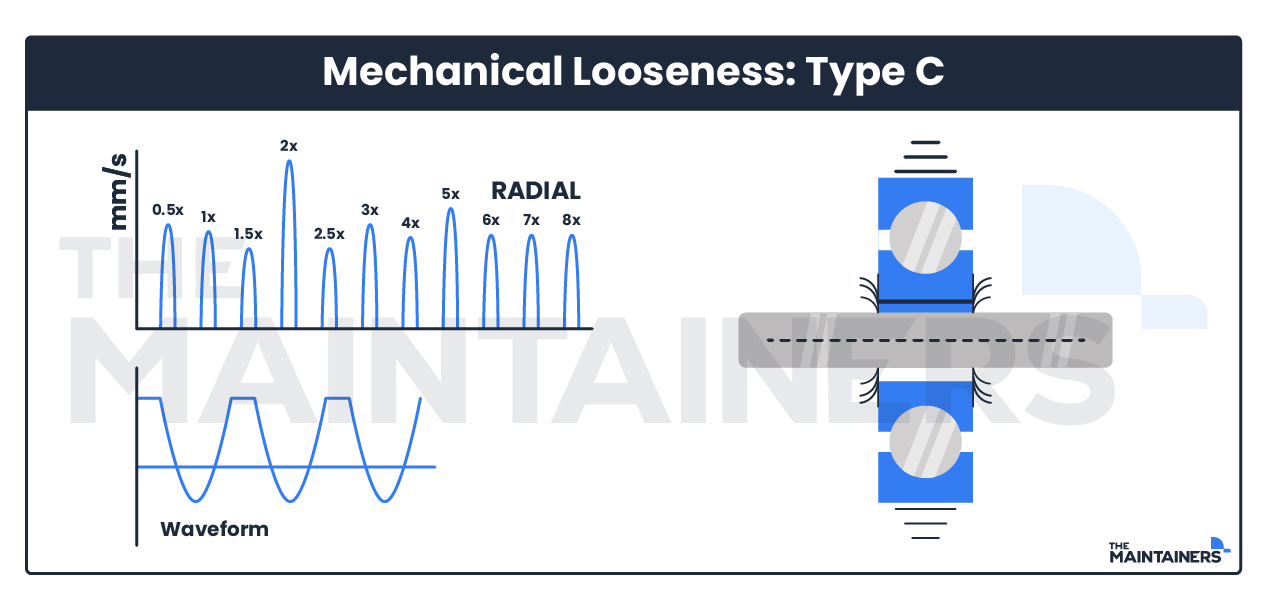
7. Transient Voltage
Also known as “surges” or “voltage spikes”, transient voltages have various origins. Adjacent loads turning on or off, power factor correction capacitor banks, or distant weather, for example, can generate transient voltages on distribution systems.
They can damage devices connected to the circuit, corrode them, or even cause the motor winding insulation to break down. This results in early motor failure and unplanned downtime.
Because the symptoms can present themselves in very different ways, it can be difficult to find the source of the problem. These surges do vary in amplitude and frequency, but are very rare.
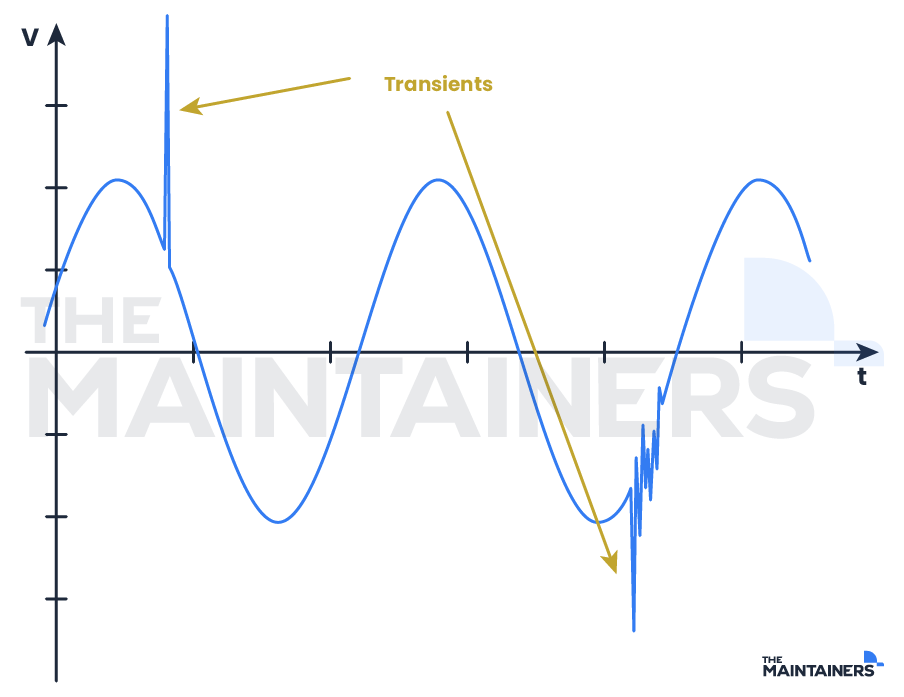
8. Harmonic Distortion
The total harmonic distortion (THD) of a current is normal on systems serving electronic loads. To analyze if these occurrences are out of the ordinary and could harm your asset, it’s necessary to investigate the source of the distortions.
Each harmonic has a different acceptable level of distortion, which is defined by standards such as IEEE 519-1992.
In this case, harmonic distortions are high-frequency components of an electrical signal, or unwanted additional sources of AC voltages or currents supplying power to the motor windings.
This energy isn’t used to rotate the motor shaft, so it circulates in the bearings – contributing to internal energy losses and heat generation. Over time, this can cause deterioration of the insulation capability of the windings.
As a result, we see problems like an increase in the asset’s operating temperature, gradual loss of motor efficiency, and additional maintenance costs.
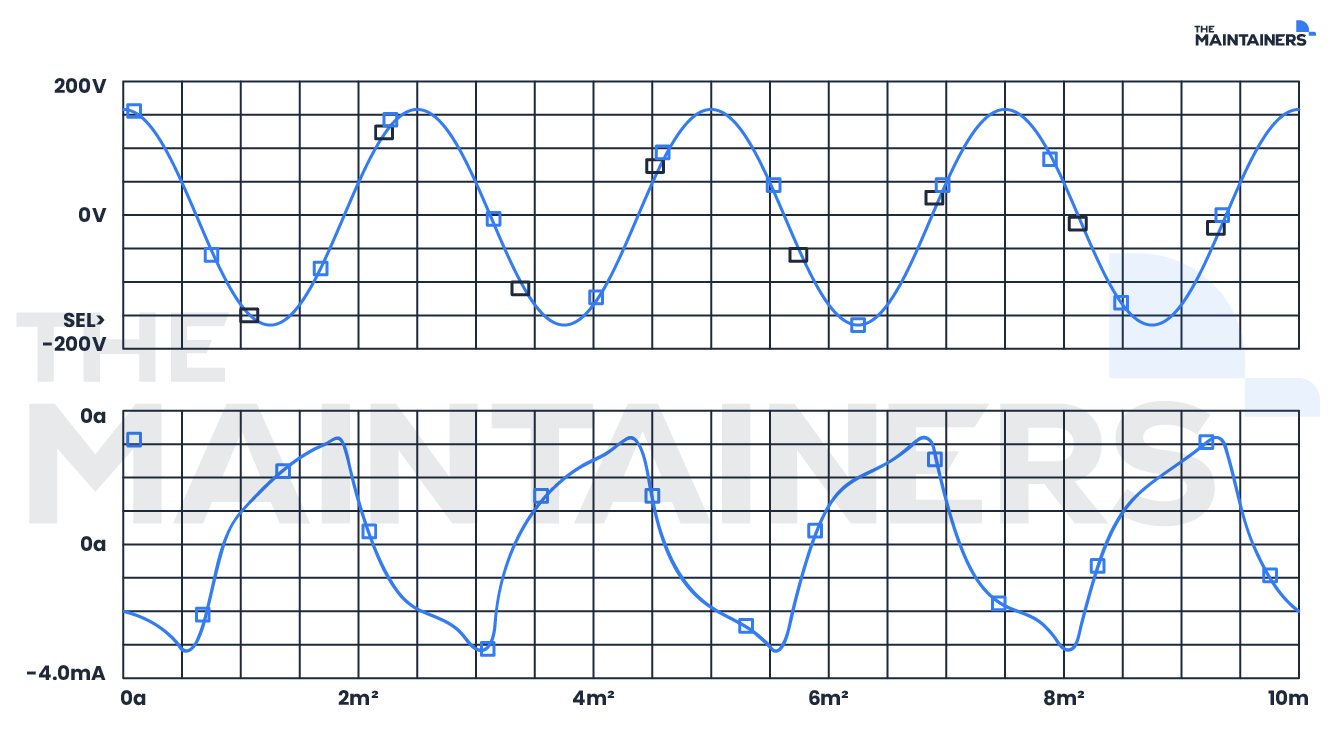
9. Sigma Current
Sigma currents are stray currents that circulate through an electrical circuit. They’re generated by frequency in the signal, voltage level, capacitances, and inductances in electrical conductors. When circulating through ground protection systems, they can cause untimely tripping and even excess heat in motor windings.
Found in the motor cables, they represent the sum of the current of the three phases at any point in time.
To prevent the problem, try using well-sized, quality conductors – try to avoid improper welding on the conductor.
10. Unbalanced Phases
To keep electric motors functioning correctly, the three phases feeding the stator must be balanced. An unbalance in impedance or load distribution can contribute to disturbing that balance.
In the industry, most three-phase distribution systems serve single-phase loads. When an unbalance happens in the impedance load distribution, the problem can ripple out to all three phases, generating an excessive current flow that increases operating temperature.
Potential faults may be in the cabling to the motor, the terminations at the motor, and potentially the windings themselves. The failure can lead to stresses in each of the phase circuits in a three-phase power system, overheating, and problems in the insulation of the motor windings.
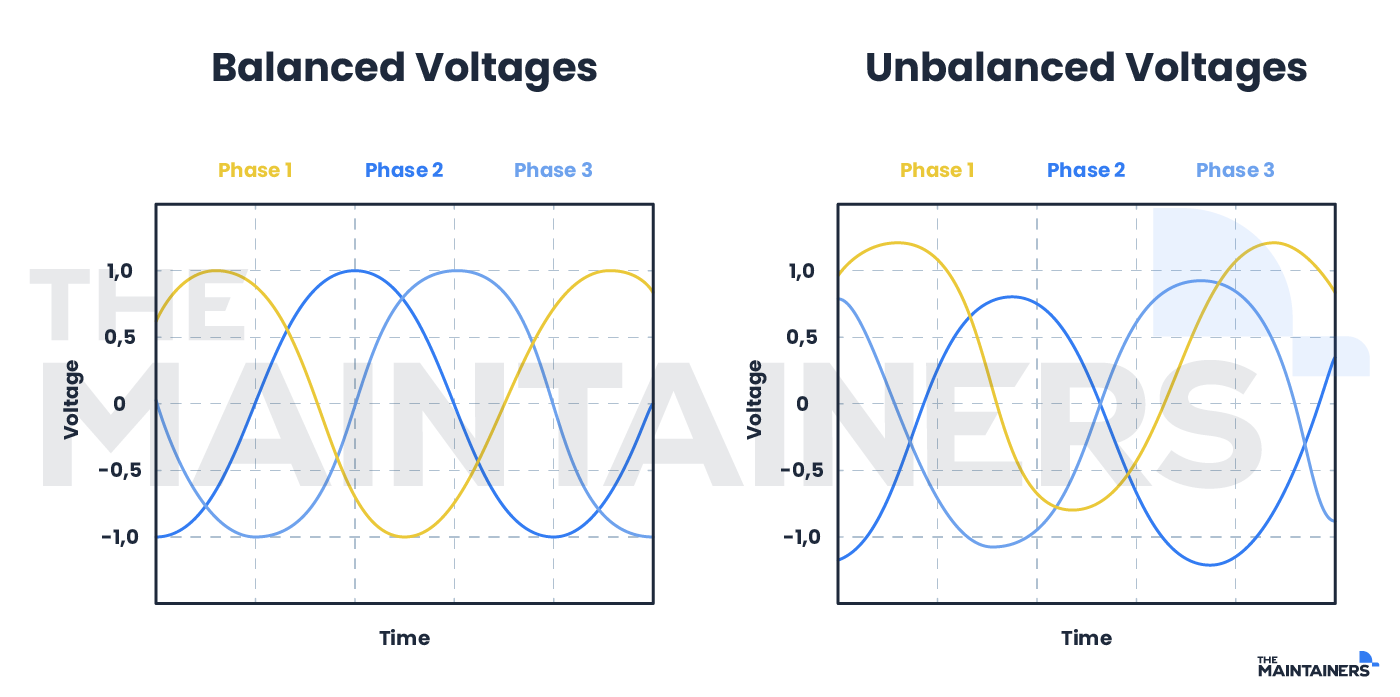